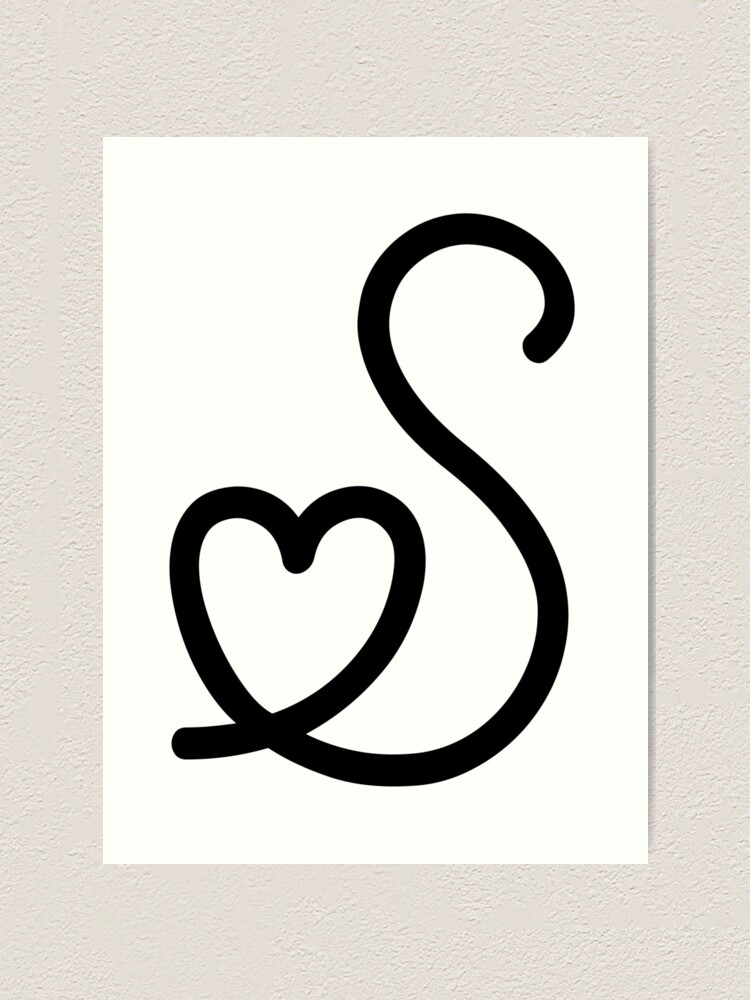
Labor relations specialists are a great career choice if you're interested in a career in the field of labor relations. While this job requires a Bachelor's degree, you can also earn a Master's degree. A labor relations specialist job specification should list preferred and required qualifications. It is important to include the details of education and certification for labor relations specialists in job descriptions.
A labor relations specialist has common duties
In addition to experience in human resources, a labor relations specialist should have strong interpersonal and problem-solving skills. The specialist must also be proficient at technology and spreadsheets. It takes just minutes to create a labor relations specialist resume. You can use our labor relations specialist resume samples as a guide when creating your own resume.
A bachelor's degree is the most common requirement for labor relations specialists. Education requirements for labor relations specialists can vary, from a high school diploma up to a master's. The labor relations specialist works to build a bridge between workers, management and the other.
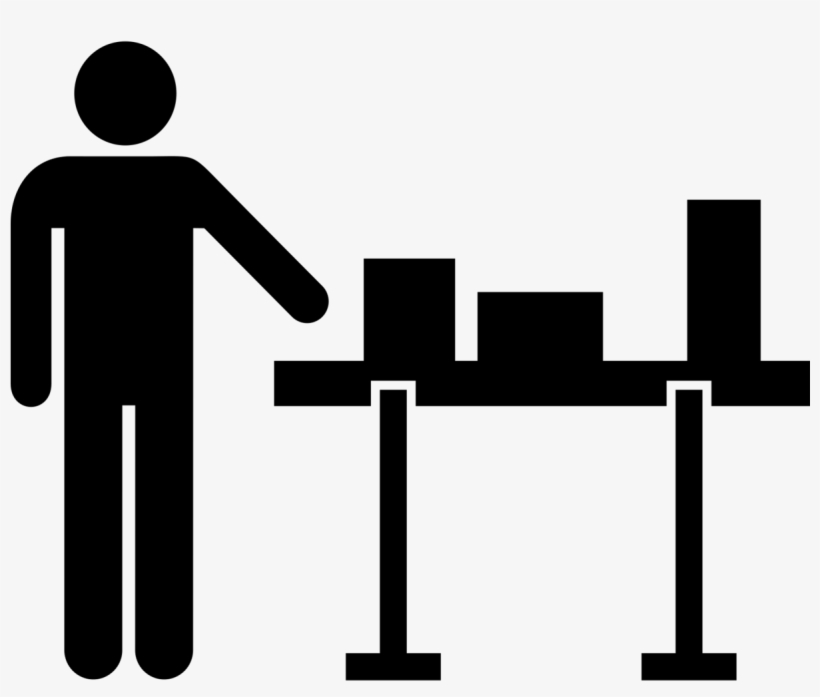
Education is necessary
It is crucial to be familiar with the employment laws before you embark on this career path. These laws include the Fair Labor Standards Act (Fair Labor Standards Act) and the National Labor Relations Act (National Labor Relations Act). A solid knowledge of these laws is necessary to become a labor relation specialist. Graduate and undergraduate courses in labor law are available. This field can also be certified. While these certifications aren't mandatory, they can help you get a better grasp of labor laws and allow you to concentrate on certain areas.
A labor relations specialist must have exceptional communication skills, regardless of their education. They must be able to communicate effectively with both employees and managers. They should also be able to resolve conflicts. As with any job, you should review a labor relations specialist job description to determine what skills and education are necessary for this position.
Potential earning
Labor relations specialists are in high demand as the 21st-century advances. While the number is declining, there are still many jobs available each year. An estimated 70,000 positions will open between now and 2029. A labor relations specialist is a great starting point if you are interested in this field. Working in other fields allows you to gain experience and earn your degree. Those who can effectively communicate with clients and manage negotiations will have an advantage over their competitors.
The earning potential of labor relations specialists is between $64,800 and $128,600. Salary ranges depend on experience and where you live. Labor relations specialists earn an average salary of $74,877 annually. New Jersey and Utilities are the most lucrative regions for labor relation specialists.
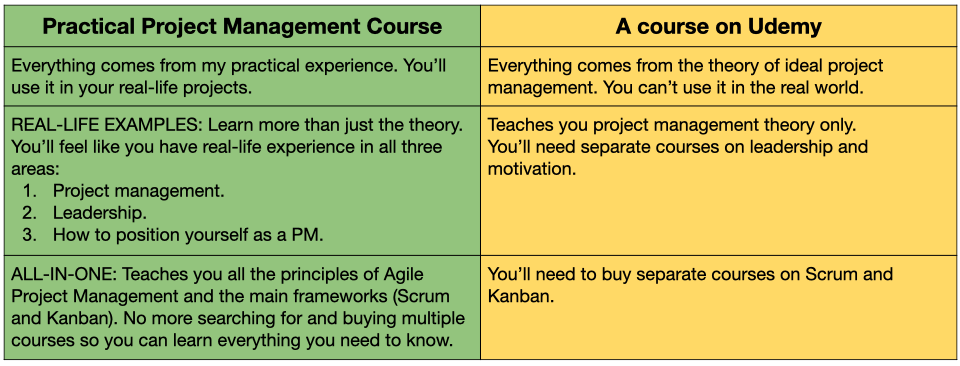
Perspectives on the job
According to the U.S. Bureau of Labor Statistics, the job outlook for labor relations specialists is generally negative. This is a result of a decline in the number of unions, which is expected to decrease employment opportunities. Candidates with specialized certification and higher education should still have the best job chances.
You can get a degree in human resource management and a bachelor's degree in labor relations. The degree is designed to help students develop leadership skills as well as the ability to manage employees. It also covers the current trends and issues in human resources, including labor relations.
FAQ
What is a management tool to help with decision-making?
A decision matrix, a simple yet powerful tool for managers to make decisions, is the best. It helps them think systematically about all the options available to them.
A decision matrix can be used to show alternative options as rows or columns. This allows one to see how each alternative impacts other options.
This example shows four options, each represented by the boxes on either side of the matrix. Each box represents an alternative. The top row displays the current situation, and the bottom row shows what might happen if nothing is done.
The effect of Option 1 can be seen in the middle column. It would translate into an increase in sales from $2million to $3million.
These are the results of selecting Options 2 or 3. These are good changes, they increase sales by $1million or $500,000. These changes can also have negative effects. Option 2 increases costs by $100 thousand, while Option 3 decreases profits to $200 thousand.
The last column displays the results of selecting Option 4. This means that sales will decrease by $1 million.
The best thing about using a decision matrix is that you don't need to remember which numbers go where. The best thing about a decision matrix is that you can simply look at the cells, and immediately know whether one option is better or not.
The matrix has already done all of the work. It is as simple a matter of comparing all the numbers in each cell.
Here is an example of how a decision matrix might be used in your business.
Advertising is a decision that you make. If you do this, you will be able to increase revenue by $5000 per month. However, additional expenses of $10 000 per month will be incurred.
If you look at the cell that says "Advertising", you can see the number $15,000. Advertising is worth much more than the investment cost.
What is the difference between a project and a program?
A program is permanent, whereas a project is temporary.
A project is usually defined by a clear goal and a set deadline.
It is often performed by a team of people, who report back on someone else.
A program is usually defined by a set or goals.
It is often done by one person.
What is the difference in Six Sigma and TQM?
The key difference between the two quality management tools is that while six-sigma focuses its efforts on eliminating defects, total quality management (TQM), focuses more on improving processes and reducing cost.
Six Sigma is a methodology for continuous improvement. It emphasizes the elimination of defects by using statistical methods such as control charts, p-charts, and Pareto analysis.
The goal of this method is to reduce variation in product output. This is done by identifying root causes and rectifying them.
Total quality management involves measuring and monitoring all aspects of the organization. It also includes the training of employees to improve performance.
It is often used as a strategy to increase productivity.
Statistics
- Your choice in Step 5 may very likely be the same or similar to the alternative you placed at the top of your list at the end of Step 4. (umassd.edu)
- The profession is expected to grow 7% by 2028, a bit faster than the national average. (wgu.edu)
- The average salary for financial advisors in 2021 is around $60,000 per year, with the top 10% of the profession making more than $111,000 per year. (wgu.edu)
- As of 2020, personal bankers or tellers make an average of $32,620 per year, according to the BLS. (wgu.edu)
- This field is expected to grow about 7% by 2028, a bit faster than the national average for job growth. (wgu.edu)
External Links
How To
How can Lean Manufacturing be done?
Lean Manufacturing processes are used to reduce waste and improve efficiency through structured methods. These processes were created by Toyota Motor Corporation, Japan in the 1980s. The aim was to produce better quality products at lower costs. Lean manufacturing is about eliminating redundant steps and activities from the manufacturing process. It is composed of five fundamental elements: continuous improvement; pull systems, continuous improvements, just-in–time, kaizen, continuous change, and 5S. The production of only what the customer needs without extra work is called pull systems. Continuous improvement involves constantly improving upon existing processes. Just-intime refers the time components and materials arrive at the exact place where they are needed. Kaizen stands for continuous improvement. Kaizen can be described as a process of making small improvements continuously. Finally, 5S stands for sort, set in order, shine, standardize, and sustain. These five elements are combined to give you the best possible results.
Lean Production System
Six key concepts make up the lean manufacturing system.
-
Flow is about moving material and information as near as customers can.
-
Value stream mapping- This allows you to break down each step of a process and create a flowchart detailing the entire process.
-
Five S's: Sort, Shine Standardize, Sustain, Set In Order, Shine and Shine
-
Kanban: Use visual signals such stickers, colored tape, or any other visual cues, to keep track your inventory.
-
Theory of constraints - identify bottlenecks in the process and eliminate them using lean tools like kanban boards;
-
Just-intime - Order components and materials at your location right on the spot.
-
Continuous improvement - make incremental improvements to the process rather than overhauling it all at once.