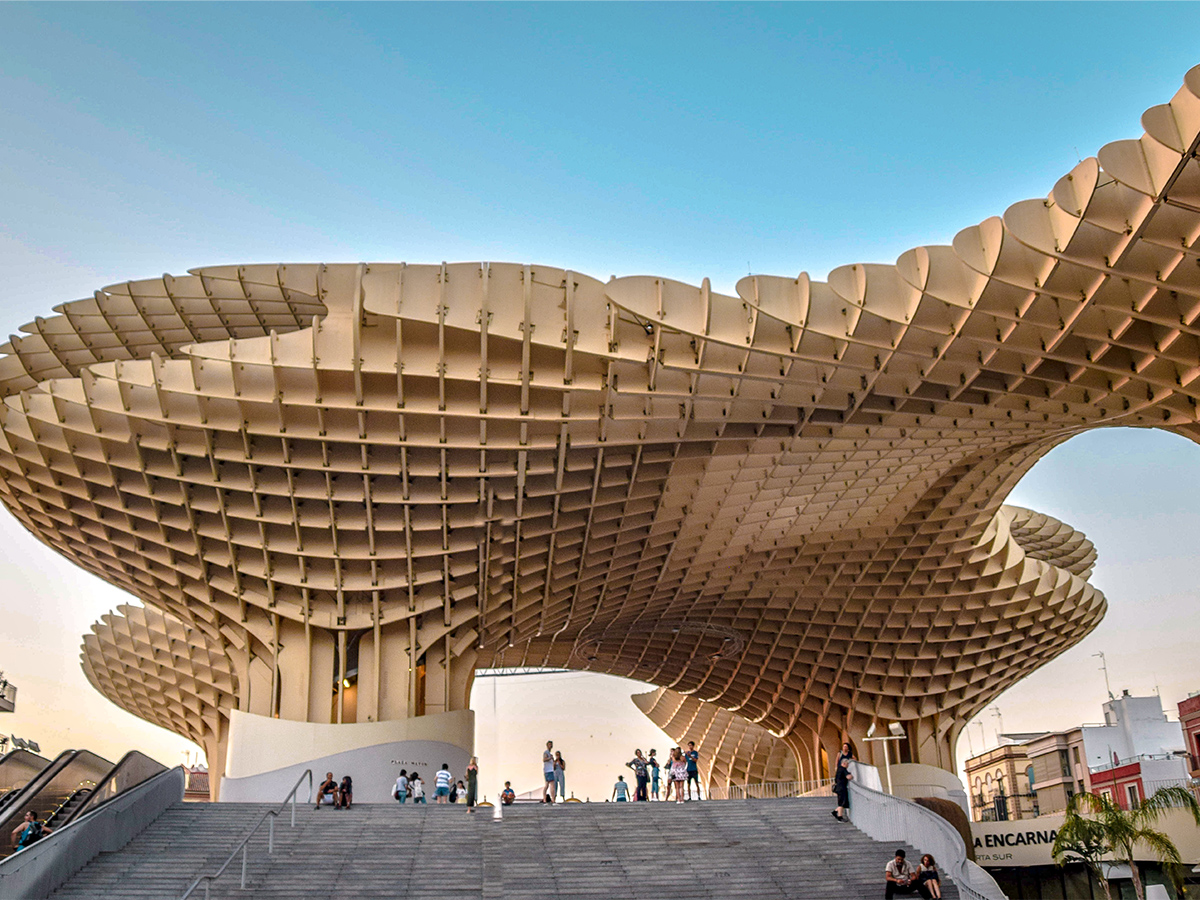
Supply chain success is based on five elements. These elements include working collaboratively with suppliers, reducing costs, and managing upstream and downstream business issues. Identifying and implementing each of these elements is vital for supply chain success. Supply chain success can also be affected by regulatory and government bodies.
Five strategies for success in supply chain
If you are looking to meet customer expectations, supply chain management is crucial to any company's success. Your supply chain strategy should be based on customer needs in order to achieve this. This means that your fulfillment experience must be consistent with what the brand promises. A brand that promises fast delivery must be able deliver on its promise. Customers pay attention to small details. They appreciate thoughtfulness, which demonstrates the thought process behind the brand.
Supply chain success must address supplier issues. Supplier issues, such as having to pay tariffs can cause delays. This can be overcome by sourcing alternative suppliers and bulk buying before tariffs are in place. A supply chain software solution is also available to help businesses overcome delays. Such software can provide precise information about inventory movements and inventory levels.
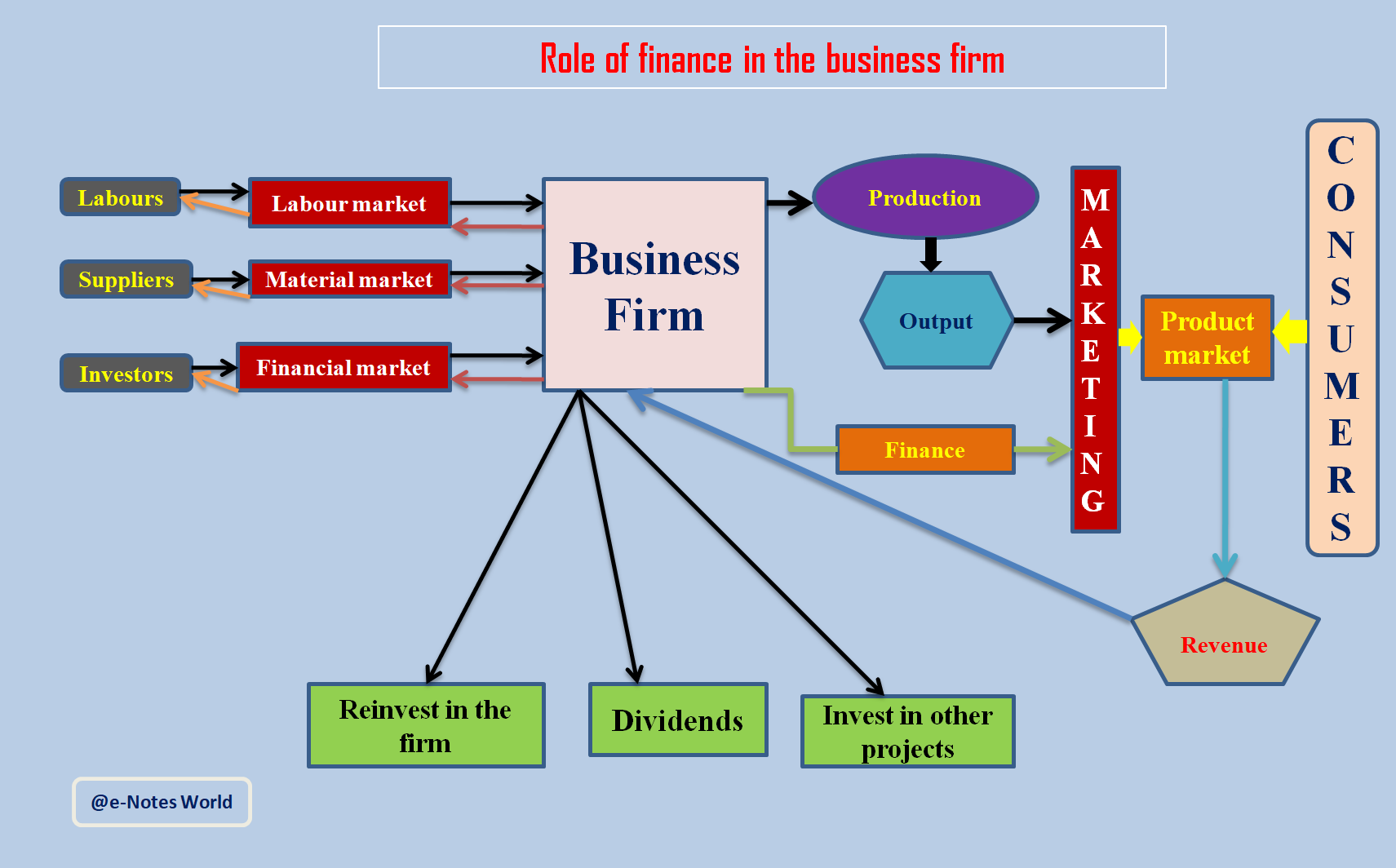
Governmental and regulatory bodies influence supply chain success
Several factors influence supply chain success, including government policies and regulations. The United States government spends federal dollar to encourage domestic capacity and develop overseas markets. While simultaneously encouraging collaboration mechanisms between domestic companies, foreign countries are also supported. These mechanisms may be private, public, or cross-government. These efforts are meant to assist companies with their dual goals, which depend on a strong and trusted global supply chain.
This is particularly important in the healthcare industry as it can have a significant impact on the supply of healthcare products. Hospitals may have to stock the correct sizes of gloves while patients may require specific medical products. Financial managers may be looking to reduce out-ofdate products and lower healthcare costs. However, others may prefer particular brands or types. The lack of coordination and alignment of incentives can disrupt the flow of supply chains.
Collaboration with suppliers
Supply chain collaboration is the process of working with suppliers to improve the efficiency of a company's procurement of goods and services. It offers many benefits to both the supplier and the customer. Collaboration is more flexible than traditional customer-supplier relationships and focuses on creating mutual value. Collaboration also allows companies to look at their suppliers as strategic partner with whom they can gain competitive advantage.
Collaboration between suppliers is crucial to the success and sustainability of a supply chain. Both parties need to look for ways to improve their relationships in order to maximize the benefits of collaboration. This can be achieved by having regular meetings with all your suppliers. This will allow you to discuss their concerns and provide constructive feedback.
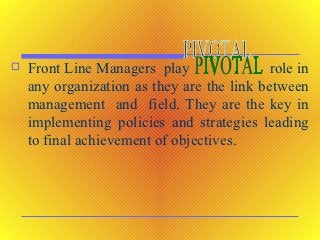
Upstream and downstream business management
Supply chain management is the integration of many processes and tasks with an emphasis on delivering value for customers and other stakeholders. This involves many risks, including legal, financial and operational. These issues can have an impact on the success or failure of a supply-chain. It is crucial to manage them.
Professionals in supply chain management must be able anticipate and predict the most important issues impacting their businesses and create strong management plans. They should also collaborate with their customers and suppliers to ensure that potential issues are addressed before they happen. It is essential that supply chain managers are proactive in dealing with global economic instability and increasing complexity. Political situations, for example, may result in tariffs being placed on trade routes. This can increase costs and take longer customs processing times. It also slows down international shipping.
FAQ
What are the steps that management takes to reach a decision?
The decision-making process of managers is complicated and multifaceted. It involves many elements, including analysis, strategy. planning. implementation. measurement. evaluation. feedback.
Management of people requires that you remember that they are just as human as you are, and can make mistakes. As such, there are always opportunities for improvement, especially when you put in the effort to improve yourself.
This video will explain how decision-making works in Management. We'll discuss the different types and reasons they are important. Managers should also know how to navigate them. Here are some topics you'll be learning about:
What's the difference between a program and a project?
A project is temporary while a programme is permanent.
A project is usually defined by a clear goal and a set deadline.
This is often done by a group of people who report to one another.
A program typically has a set goal and objective.
It is usually implemented by a single person.
What is the difference in Six Sigma and TQM?
The main difference between these two quality-management tools is that six-sigma concentrates on eliminating defects while total QM (TQM), focuses upon improving processes and reducing expenses.
Six Sigma is a method for continuous improvement. This method emphasizes eliminating defects using statistical methods such p-charts, control charts, and Pareto analysis.
This method has the goal to reduce variation of product output. This is achieved by identifying and addressing the root causes of problems.
Total quality management refers to the monitoring and measurement of all aspects in an organization. It also includes training employees to improve performance.
It is used to increase productivity.
How do we create a company culture that is productive?
A culture of respect and value within a company is key to a productive culture.
It is based on three principles:
-
Everybody has something of value to share
-
Fair treatment of people is the goal
-
Respect is shared between individuals and groups
These values are reflected in the way people behave. They will treat others with consideration and courtesy.
They will respect other people's opinions.
They can also be a source of inspiration for others.
Company culture also encourages open communication, collaboration, and cooperation.
People feel comfortable expressing their opinions freely without fear of reprisal.
They know mistakes will be accepted as long as they are dealt with honestly.
Finally, the company culture promotes integrity and honesty.
Everyone knows that they must always tell truth.
Everyone understands there are rules that they must follow.
And no one expects special treatment or favors.
What can a manager do to improve his/her management skillset?
By practicing good management skills at all times.
Managers need to monitor their subordinates' performance.
It is important to take immediate action if your subordinate doesn't perform as expected.
It is essential to know what areas need to be improved and how to do it.
How can a manager motivate employees?
Motivation is the desire to do well.
Engaging in something fun can be a great way to get motivated.
Another way to get motivated is to see yourself as a contributor to the success of the company.
You might find it more rewarding to treat patients than to study medical books if you plan to become a doctor.
The inner motivation is another type.
For example, you might have a strong sense of responsibility to help others.
Maybe you like working hard.
If you don’t feel motivated, find out why.
You can then think of ways to improve your motivation.
Statistics
- This field is expected to grow about 7% by 2028, a bit faster than the national average for job growth. (wgu.edu)
- Your choice in Step 5 may very likely be the same or similar to the alternative you placed at the top of your list at the end of Step 4. (umassd.edu)
- As of 2020, personal bankers or tellers make an average of $32,620 per year, according to the BLS. (wgu.edu)
- The average salary for financial advisors in 2021 is around $60,000 per year, with the top 10% of the profession making more than $111,000 per year. (wgu.edu)
- Hire the top business lawyers and save up to 60% on legal fees (upcounsel.com)
External Links
How To
How do you implement a Quality Management Plan (QMP)?
The Quality Management Plan (QMP) was established in ISO 9001. It is a systematic way to improve processes, products and services. It emphasizes on how to continuously measure, analyze, control, and improve processes, product/service, and customer satisfaction.
QMP is a method that ensures good business performance. QMP helps improve production, service delivery and customer relationships. QMPs should cover all three dimensions - Products, Processes, and Services. If the QMP only covers one aspect, it's called a "Process QMP". If the QMP is focused on a product/service, it's called a QMP. And when the QMP concentrates on Customer Relationships, it is called "Customer" QMP.
There are two key elements to implementing a QMP: Strategy and Scope. These elements can be defined as follows.
Scope is what the QMP covers and how long it will last. For example, if you want to implement a QMP that lasts six months, then this scope will outline the activities done during the first six.
Strategy: This describes how you will achieve the goals in your scope.
A typical QMP includes five phases: Design, Planning, Development and Implementation. Each phase is explained below:
Planning: In this stage the QMP's objectives and priorities are established. All stakeholders involved in the project are consulted to understand their requirements and expectations. After identifying the objectives, priorities and stakeholder involvement, it's time to develop the strategy for achieving the goals.
Design: The design stage involves the development of vision, mission strategies, tactics, and strategies that will allow for successful implementation. These strategies can be implemented through the creation of detailed plans.
Development: Here, the team develops the resources and capabilities that will support the successful implementation.
Implementation: This refers to the actual implementation or the use of the strategies planned.
Maintenance: Maintaining the QMP over time is an ongoing effort.
Additional items must be included in QMP.
Participation by Stakeholders is essential for the QMP's continued success. They should be involved in planning, design, development and implementation of the QMP.
Initiation of a Project: A clear understanding and application of the problem statement is crucial for initiating a project. Also, the initiator should understand why they are doing it and what they expect.
Time frame: The QMP's timeframe is critical. You can use a simplified version if you are only going to be using the QMP for short periods. However, if you have a long-term commitment, you may require more elaborate versions.
Cost Estimation. Cost estimation is another crucial component of QMP. It is impossible to plan without knowing what you will spend. The QMP should be cost-estimated before it can begin.
The most important thing about a QMP is that it is not just a document but also a living document. It changes as the company grows. It is important to review it periodically to ensure it meets all current requirements.