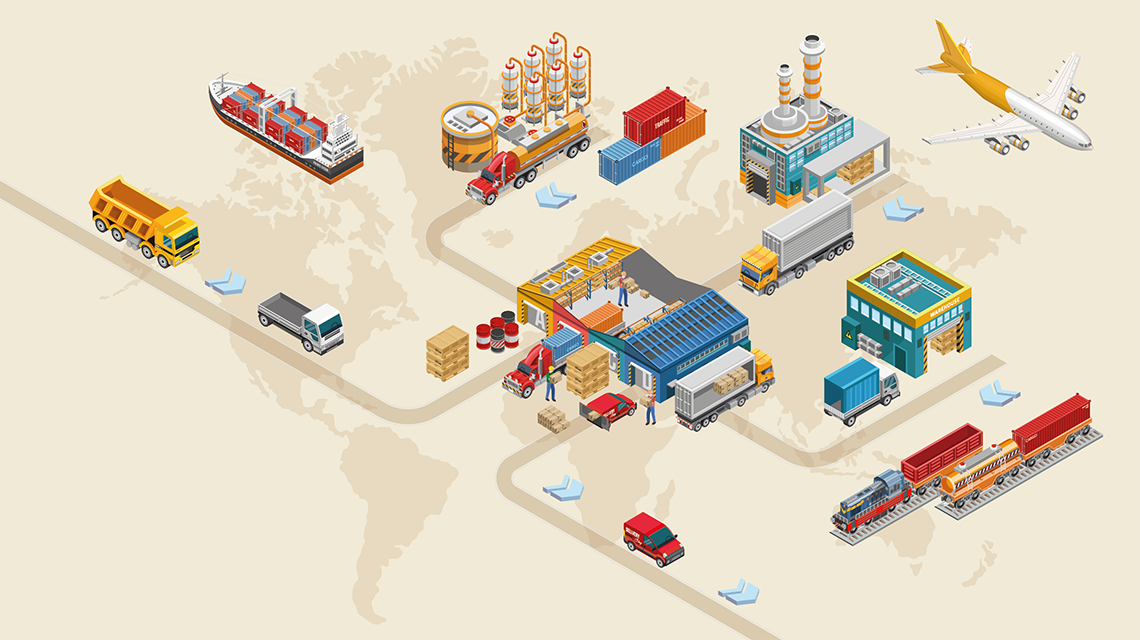
ANN-based forecasting
Artificial neural networks (ANNs) are widely used in business to improve forecasting. Various techniques have been developed to make ANNs more accurate. A new study aims to apply ANNs for Supply Chain Management. It compares the performance of four different ANN models: the FSANN, FWANN, and HYANN. HYANN is a combination FWANN/FSANN. It incorporates feature selection (and feature weighting) to improve performance.
Neural networks are composed of many interconnected layers. Each layer is made up of a number neurons. The input layer receives external data, while the output layer returns results. The hidden layer is made up of neurons that can be used to refine the results. While the number or neurons in the input layers and output layers is predetermined, the hidden layer may contain a variety of neurons. It depends on how many layers are hidden, whether there are bias neurons or not, and what the learning rate is.
Probabilistic forecasting
Probabilistic prediction can be applied in many areas of supply chain management. Its main goal is to reduce the uncertainty associated with making decisions. It is crucial to take into account all sources of uncertainty, even those that may not be easily quantifiable. This approach can be used to help companies plan their inventory.
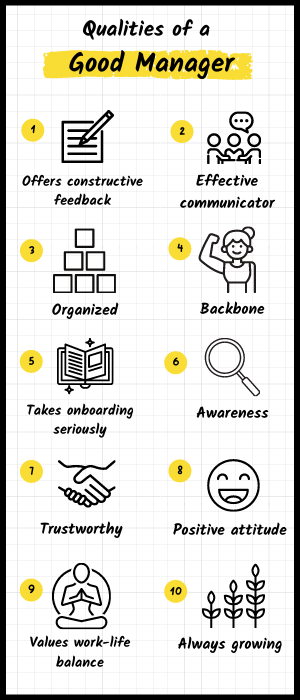
A probabilistic forecast involves creating different scenarios for different outcomes. It can be affected by uncertainties such as uncertain customer returns, lead times, and uncertain demand. You can also think about the uncertainty surrounding when an order will arrive from a supplier. It is possible to assess the uncertainty involved in these scenarios manually by having a detailed understanding of the context.
Regression analysis
Forecasting supply chain management may be hard. However, regression analysis could help. It forces businesses to analyze actual data. If a company wants to know the rainy season, they can plot sales versus rainfall for the past three years. This will provide a visual representation of peak sales.
Forecasting the demand of a particular product requires a statistical modeling that uses past data. The model is then refined by adding current data and testing it with known historical data. Only then can the forecasting model be used to predict future trends. Supply chain managers need to be aware of the limitations of supply chain forecasting models.
AI
Artificial Intelligence (AI) can be disruptive technology and help supply chain managers to anticipate future requirements. It can also reduce processing time. AI also allows smarter decisionmaking. It offers valuable insights into market trends, weather patterns and other variables. These data can have a significant impact on customer relations and industry credibility. It can help companies understand where bottlenecks are and why they occur.
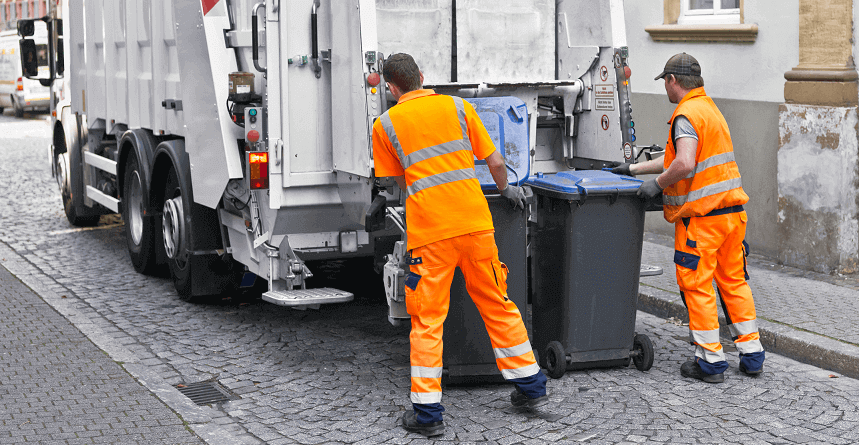
AI forecasting helps improve supply chain management. It can also optimize the forecasting process by examining historical data and current trends, such as social media chatter. AI can assist logistics operators to determine the demand for goods and services by analysing this data.
FAQ
Why does it sometimes seem so hard to make good business decisions
Complex systems with many moving parts are the hallmark of businesses. They require people to manage multiple priorities and deal with uncertainty and complexity.
The key to making good decisions is to understand how these factors affect the system as a whole.
You need to be clear about the roles and responsibilities of each system. Then, you need to think about how these pieces interact with one another.
It is also worth asking yourself if you have any unspoken assumptions about how you have been doing things. If you don't have any, it may be time to revisit them.
If you're still stuck after all this, try asking someone else for help. You may be able to see things from a different perspective than you are and gain insight that can help you find a solution.
What do we mean when we say "project management"?
It refers to the management of activities related to a project.
Our services include the definition of the scope, identifying requirements, preparing a budget, organizing project teams, scheduling work, monitoring progress and evaluating the results before closing the project.
What are the top management skills?
Any business owner needs to be able to manage people, finances, resources and time. These include the ability and willingness to manage people, finances as well resources, time and space.
Managerial skills are required when setting goals and objectives and planning strategies, leading employees, motivating them, solving problems, creating policies, procedures, or managing change.
As you can see, there's no end to the list of managerial duties!
How can we create a culture of success in our company?
Successful company culture is one where people feel valued and respected.
It's based on three main principles:
-
Everyone has something valuable to contribute
-
People are treated with respect
-
Respect is shared between individuals and groups
These values are evident in the way that people act. They will treat others with respect and kindness.
They will be respectful of the opinions of other people.
They can also be a source of inspiration for others.
Company culture also encourages open communication, collaboration, and cooperation.
People feel comfortable expressing their opinions freely without fear of reprisal.
They are aware that mistakes can be accepted if they are treated honestly.
Finally, the company culture promotes integrity and honesty.
Everyone knows that they must always tell the truth.
Everyone recognizes that rules and regulations are important to follow.
Nobody expects to be treated differently or given favors.
What are some common mistakes managers make when managing people?
Sometimes managers make their job harder than they need to.
They might not give enough support and delegate the right responsibilities to their staff.
A majority of managers lack the communication skills needed to motivate their team and lead them.
Managers sometimes set unrealistic expectations of their teams.
Managers may prefer to solve every problem for themselves than to delegate responsibility.
How do you effectively manage employees?
Managing employees effectively means ensuring that they are happy and productive.
It also means having clear expectations of their behavior and keeping track of their performance.
Managers need clear goals to be able to accomplish this.
They should communicate clearly with employees. They need to communicate clearly with their staff.
They also need to keep records of their team's activities. These include:
-
What was achieved?
-
How much work did you put in?
-
Who did it, anyway?
-
What was the moment it was completed?
-
Why was it done?
This information can help you monitor your performance and to evaluate your results.
How does Six Sigma work
Six Sigma uses statistics to measure problems, find root causes, fix them, and learn from past mistakes.
The first step is to identify the problem.
The next step is to collect data and analyze it in order to identify trends or patterns.
The problem is then rectified.
Finally, the data are reanalyzed in order to determine if it has been resolved.
This cycle will continue until the problem is solved.
Statistics
- As of 2020, personal bankers or tellers make an average of $32,620 per year, according to the BLS. (wgu.edu)
- Your choice in Step 5 may very likely be the same or similar to the alternative you placed at the top of your list at the end of Step 4. (umassd.edu)
- The profession is expected to grow 7% by 2028, a bit faster than the national average. (wgu.edu)
- The average salary for financial advisors in 2021 is around $60,000 per year, with the top 10% of the profession making more than $111,000 per year. (wgu.edu)
- 100% of the courses are offered online, and no campus visits are required — a big time-saver for you. (online.uc.edu)
External Links
How To
How can you use the Kaizen method?
Kaizen means continuous improvement. This term was first used by Toyota Motor Corporation in the 1950s. It refers to the Japanese philosophy that emphasizes continuous improvement through small incremental changes. It's a team effort to continuously improve processes.
Kaizen is one of Lean Manufacturing's most efficient methods. The concept involves employees responsible for manufacturing identifying problems and trying to fix them before they become serious issues. This way, the quality of products increases, and the cost decreases.
Kaizen is an approach to making every worker aware and alert to what is happening around them. It is important to correct any problems immediately if they are discovered. So, if someone notices a problem while working, he/she should report it to his/her manager.
Kaizen follows a set of principles. Start with the end product, and then move to the beginning. If we want to improve our factory for example, we start by fixing the machines that make the final product. Next, we fix the machines which produce components. Then, we fix those who work directly with the machines.
This method, called 'kaizen', focuses on improving each and every step of the process. Once the factory is fixed, we return to the original site and work our way back until we get there.
Before you can implement kaizen into your business, it is necessary to learn how to measure its effectiveness. There are many methods to assess if kaizen works well. One method is to inspect the finished products for defects. Another way is to check how much productivity has grown since kaizen was implemented.
A good way to determine whether kaizen has been implemented is to ask why. You were trying to save money or obey the law? Did you really believe it would lead to success?
If you answered yes to any one of these questions, congratulations! You're ready to start kaizen.