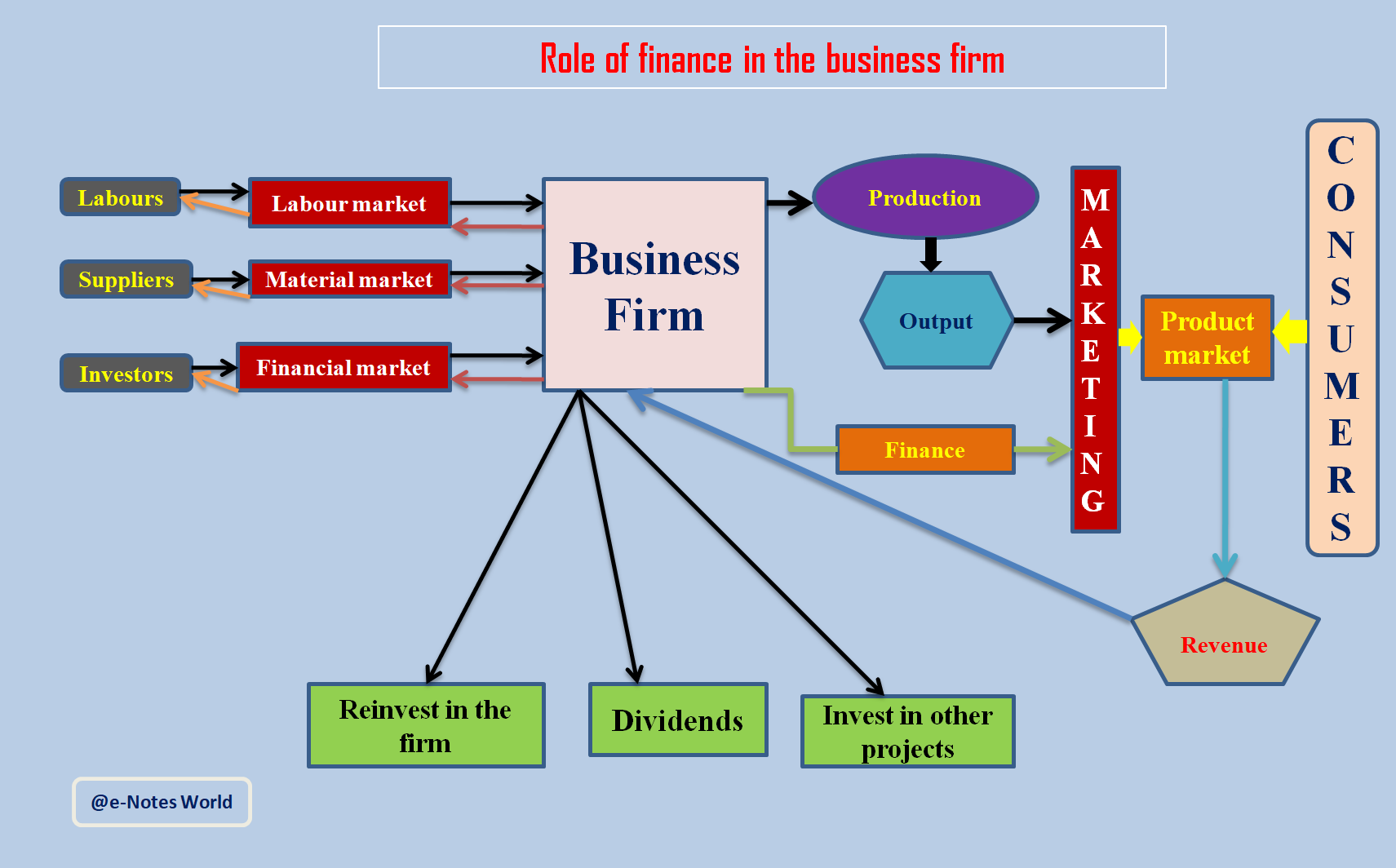
Mismanagement is when you make a mess of something that you're running. It can be anything from spending money on the wrong things to breaching a contract or legal obligation. In some cases, mismanagement can also be a result of a conflict of opinion. Here are some examples. Here are some examples of workplace mismanagement.
It is a matter of differing opinions
Mismanagement refers to activities that are perceived as a waste. This label can often be associated with grudges. The result is less money available to fund pet projects. Common examples include spending "too much" on internationalization, prioritizing a field of study over another field, or constructing a new building. However, mismanagement can also arise from disagreements regarding institutional goals.
It can be considered a breach or contract violation.
Mismanagement is any type of business practice that results in a breach of contractual or legal obligations. Most business contracts are meant to benefit all involved. However, it is possible for delays, financial problems and other unexpected circumstances to prevent a contract from being completed as agreed. When this happens, the parties involved can sue each other for breach of contract.
FAQ
What are some common mistakes managers make when managing people?
Managers sometimes make their own job harder than necessary.
They might not give enough support and delegate the right responsibilities to their staff.
In addition, many managers lack the communication skills required to motivate and lead their teams.
Some managers create unrealistic expectations for their teams.
Managers may prefer to solve every problem for themselves than to delegate responsibility.
What's the difference between Six Sigma and TQM?
The main difference between these two quality-management tools is that six-sigma concentrates on eliminating defects while total QM (TQM), focuses upon improving processes and reducing expenses.
Six Sigma is an approach for continuous improvement. This method emphasizes eliminating defects using statistical methods such p-charts, control charts, and Pareto analysis.
This method aims to reduce variation in product production. This is accomplished by identifying the root cause of problems and fixing them.
Total quality management is the measurement and monitoring of all aspects within an organization. This includes training employees to improve their performance.
It is frequently used as an approach to increasing productivity.
What are management concepts?
Management concepts are the fundamental principles and practices that managers use when managing people and their resources. These topics include job descriptions, performance evaluations and training programs. They also cover human resource policies, job description, job descriptions, job descriptions, employee motivation, compensation systems, organizational structures, and many other topics.
What role should a manager play within a company
The role of a manager varies from one industry to another.
The manager oversees the day-to-day activities of a company.
He/she ensures the company meets its financial commitments and produces goods/services that customers demand.
He/she is responsible for ensuring that employees comply with all regulations and follow quality standards.
He/she oversees marketing campaigns and plans new products.
How to effectively manage employees
Managing employees effectively means ensuring that they are happy and productive.
This also involves setting clear expectations and monitoring their performance.
Managers need to establish clear goals for their team and for themselves.
They should communicate clearly to staff members. They also need to make sure that they discipline and reward the best performers.
They must also keep records of team activities. These include:
-
What was the result?
-
How much work did you put in?
-
Who did it?
-
Was it done?
-
Why it was done?
This information can be used to monitor performance and evaluate results.
How can we make our company culture successful?
A positive company culture creates a sense of belonging and respect in its people.
It's built on three fundamental principles:
-
Everybody can contribute something valuable
-
Fair treatment of people is the goal
-
There is mutual respect between individuals and groups
These values can be seen in the behavior of people. They will treat others with respect and kindness.
They will listen respectfully to the opinions of others.
They encourage others to express their feelings and ideas.
A company culture encourages collaboration and communication.
People feel safe to voice their opinions without fear of reprisal.
They are aware that mistakes can be accepted if they are treated honestly.
Finally, the company culture promotes integrity and honesty.
Everyone is aware that truth must be told.
Everyone is aware that rules and regulations apply to them.
Nobody expects to be treated differently or given favors.
Statistics
- The average salary for financial advisors in 2021 is around $60,000 per year, with the top 10% of the profession making more than $111,000 per year. (wgu.edu)
- As of 2020, personal bankers or tellers make an average of $32,620 per year, according to the BLS. (wgu.edu)
- This field is expected to grow about 7% by 2028, a bit faster than the national average for job growth. (wgu.edu)
- The BLS says that financial services jobs like banking are expected to grow 4% by 2030, about as fast as the national average. (wgu.edu)
- UpCounsel accepts only the top 5 percent of lawyers on its site. (upcounsel.com)
External Links
How To
What is Lean Manufacturing?
Lean Manufacturing techniques are used to reduce waste while increasing efficiency by using structured methods. They were developed by Toyota Motor Corporation in Japan during the 1980s. The aim was to produce better quality products at lower costs. Lean manufacturing eliminates unnecessary steps and activities from a production process. It consists of five basic elements: pull systems, continuous improvement, just-in-time, kaizen (continuous change), and 5S. It is a system that produces only the product the customer requests without additional work. Continuous improvement is constantly improving upon existing processes. Just-intime refers the time components and materials arrive at the exact place where they are needed. Kaizen means continuous improvement, which is achieved by implementing small changes continuously. Five-S stands for sort. It is also the acronym for shine, standardize (standardize), and sustain. These five elements are combined to give you the best possible results.
Lean Production System
Six key concepts form the foundation of the lean production system:
-
Flow is about moving material and information as near as customers can.
-
Value stream mapping is the ability to divide a process into smaller tasks, and then create a flowchart that shows the entire process.
-
Five S's – Sort, Put In Order Shine, Standardize and Sustain
-
Kanban - visual cues such as stickers or colored tape can be used to track inventory.
-
Theory of constraints - identify bottlenecks in the process and eliminate them using lean tools like kanban boards;
-
Just-in-time delivery - Deliver components and materials right to your point of use.
-
Continuous improvement is making incremental improvements to your process, rather than trying to overhaul it all at once.