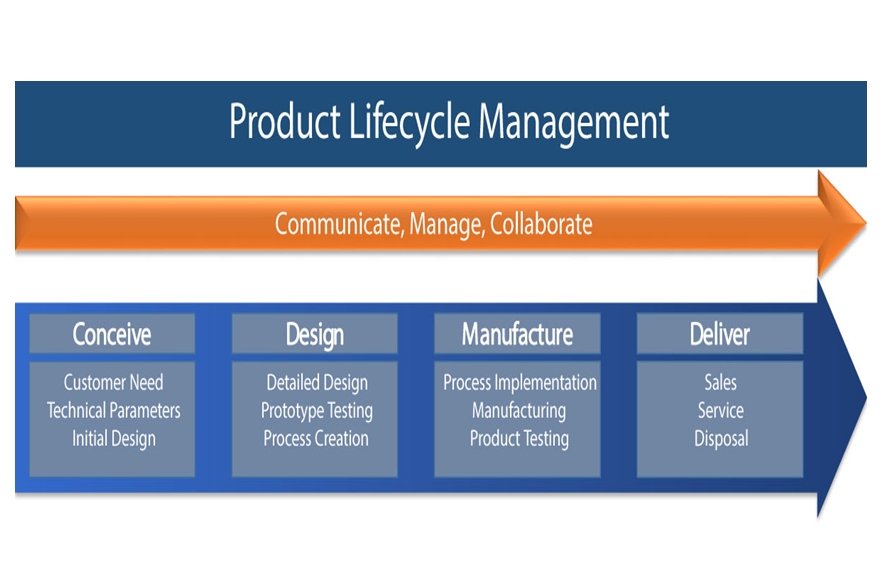
You don't have to be a perfectionist to meet deadlines. There are many ways you can stay on track and organized. A detailed schedule is the first step. You must also understand the expectations of the client or employer. It is important to not be distracted. You can plan your time based on what you expect.
Setting clear expectations
Establishing clear expectations is a great way to engage your staff. Employees want the expectation that they will succeed and that their efforts are important. You can build unity within your team by setting clear expectations and avoid any bottlenecks.
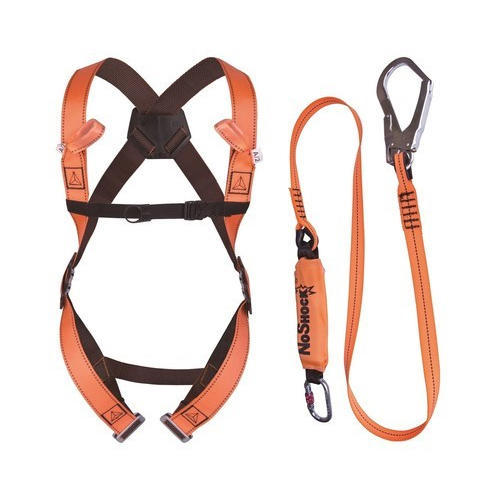
Setting up a regular alarm
The first step to creating an alarm is choosing the type of alarm. You can choose from an exact repeating alarm or an inexact one, depending on what app you are using. Inexact repeating alerts will not allow you meet specific deadlines but are less precise. They also decrease battery consumption.
Avoid distractions
It is crucial to recognize and avoid distractions in order to meet deadlines. A clear schedule and prioritizing tasks will help you concentrate on them and prevent distractions. So that you can effectively manage your time, it is important to set time limits. It is a waste of time to switch between tasks.
Monitoring progress
When it comes to deadline-oriented projects, it is important to keep track of the progress. To achieve this goal, you can create a checklist. This should include brief descriptions of each task along with its function. This will keep you motivated and focused as you work. A color-coded system is also available to help distinguish tasks.
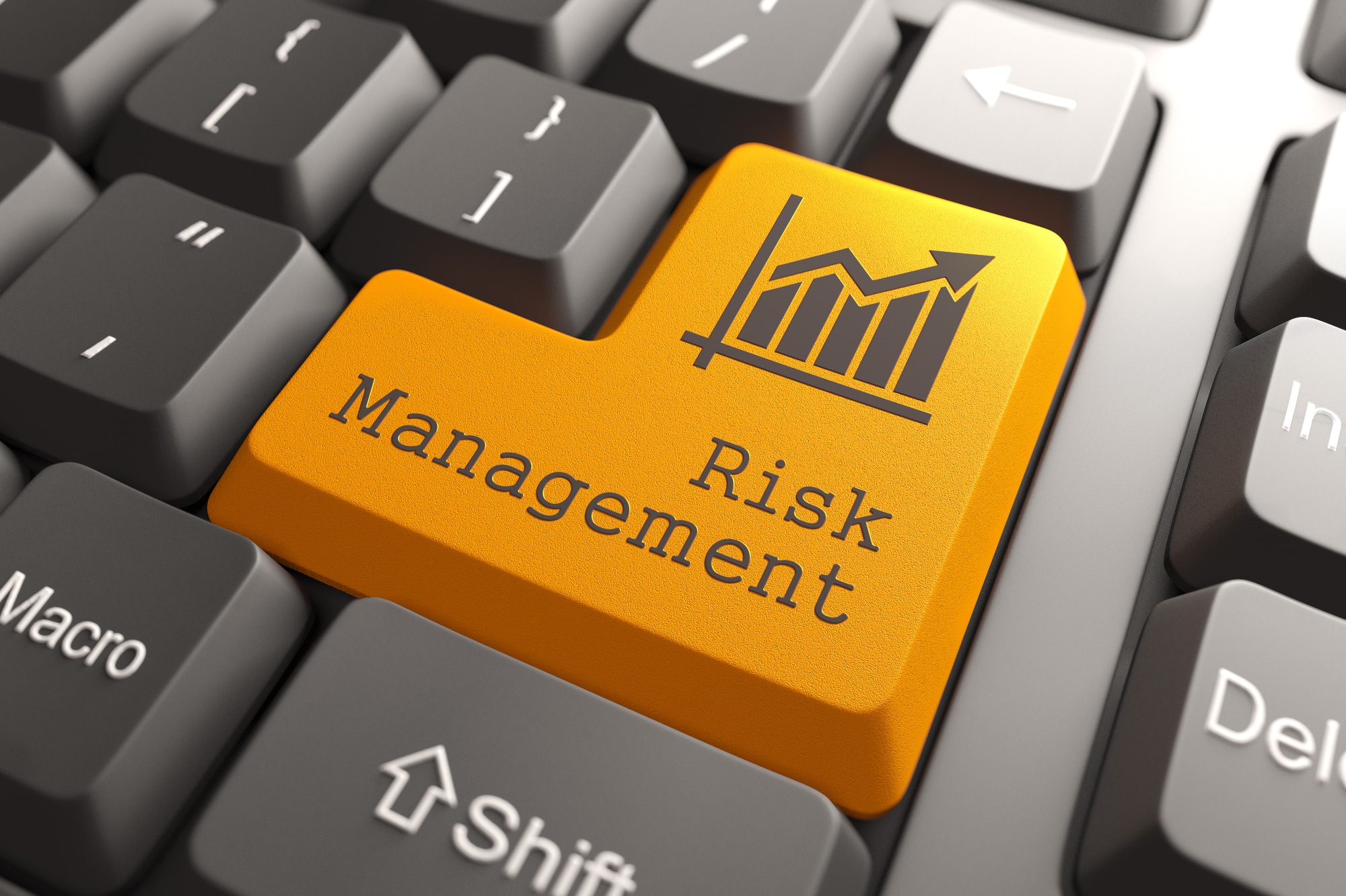
Create a Gantt Chart
Gantt charts are an excellent way of visualizing the project's timeline. You can personalize the chart to suit your needs as well as the needs of your colleagues. You can use different colors in each task bar to show different team members or to indicate different phases of a project.
FAQ
What kind of people use Six Sigma
Six Sigma is well-known to those who have worked in operations research and statistics. However, anyone involved in any aspect of business can benefit from using it.
This requires a lot of dedication, so only people with great leadership skills can make the effort to implement it.
How does a manager learn to manage?
By practicing good management skills at all times.
Managers must continuously monitor the performance levels of their subordinates.
If you notice your subordinate isn't performing up to par, you must take action quickly.
You should be able to identify what needs improvement and how to improve things.
What are the main four functions of management
Management is responsible for planning, organizing, directing, and controlling people and resources. Management also involves setting goals and developing policies.
Management helps an organization achieve its objectives by providing direction, coordination, control, leadership, motivation, supervision, training, and evaluation.
The four main functions of management are:
Planning - This is the process of deciding what should be done.
Organizing: Organizing refers to deciding how things should work.
Direction - This is the art of getting people to follow your instructions.
Controlling: Controlling refers to making sure that people do what they are supposed to.
What are the five management processes?
Each business has five stages: planning, execution and monitoring.
Setting goals for the future requires planning. Planning involves defining your goals and how to get there.
Execution happens when you actually do the plan. You need to make sure they're followed by everyone involved.
Monitoring allows you to monitor your progress towards achieving your goals. This should involve regular reviews of performance against targets and budgets.
Review events take place at each year's end. These reviews allow you to evaluate whether the year was successful. If not there are changes that can be made to improve the performance next year.
After the annual review, evaluation takes place. It helps you identify the successes and failures. It also provides feedback regarding how people performed.
What role does a manager play in a company?
Different industries have different roles for managers.
In general, a manager controls the day-to-day operations of a company.
He/she ensures that the company meets its financial obligations and produces goods or services that customers want.
He/she ensures employees adhere to all regulations and quality standards.
He/she plans new products and services and oversees marketing campaigns.
How do we build a culture that is successful in our company?
A positive company culture creates a sense of belonging and respect in its people.
It is based on three principles:
-
Everybody can contribute something valuable
-
People are treated fairly
-
Respect is shared between individuals and groups
These values are reflected in the way people behave. They will treat others with kindness and consideration.
They will respect other people's opinions.
And they will encourage others to share ideas and feelings.
Additionally, the company culture encourages open communication as well as collaboration.
People feel safe to voice their opinions without fear of reprisal.
They understand that mistakes can be forgiven as long as they're dealt with honestly.
The company culture promotes honesty, integrity, and fairness.
Everyone knows that they must always tell truth.
Everyone understands that there are rules and regulations which apply to them.
And no one expects special treatment or favors.
Statistics
- Hire the top business lawyers and save up to 60% on legal fees (upcounsel.com)
- The profession is expected to grow 7% by 2028, a bit faster than the national average. (wgu.edu)
- Our program is 100% engineered for your success. (online.uc.edu)
- As of 2020, personal bankers or tellers make an average of $32,620 per year, according to the BLS. (wgu.edu)
- Your choice in Step 5 may very likely be the same or similar to the alternative you placed at the top of your list at the end of Step 4. (umassd.edu)
External Links
How To
How can you use the Kaizen method?
Kaizen means continuous improvement. This Japanese term refers to the Japanese philosophy of continuous improvement that emphasizes incremental improvements and constant improvement. It's where people work together in order to improve their processes constantly.
Kaizen is one method that Lean Manufacturing uses to its greatest advantage. This concept requires employees to identify and solve problems during manufacturing before they become major issues. This increases the quality of products and reduces the cost.
The main idea behind kaizen is to make every worker aware of what happens around him/her. If something is wrong, it should be corrected immediately so that no problem occurs. So, if someone notices a problem while working, he/she should report it to his/her manager.
When doing kaizen, there are some principles we must follow. When working with kaizen, we always start with the end result and move towards the beginning. For example, if we want to improve our factory, we first fix the machines that produce the final product. We then fix the machines producing components, and the machines producing raw materials. And finally, we fix the workers who work directly with those machines.
This is known as "kaizen", because it emphasizes improving each step. Once the factory is fixed, we return to the original site and work our way back until we get there.
To implement kaizen in your business, you need to find out how to measure its effectiveness. There are many methods to assess if kaizen works well. One method is to inspect the finished products for defects. Another way is to check how much productivity has grown since kaizen was implemented.
To determine if kaizen is effective, you should ask yourself why you chose to implement kaizen. Did you do it because it was legal or to save money? Did you really think that it would help you achieve success?
Let's say you answered yes or all of these questions. Congratulations! You're now ready to get started with kaizen.