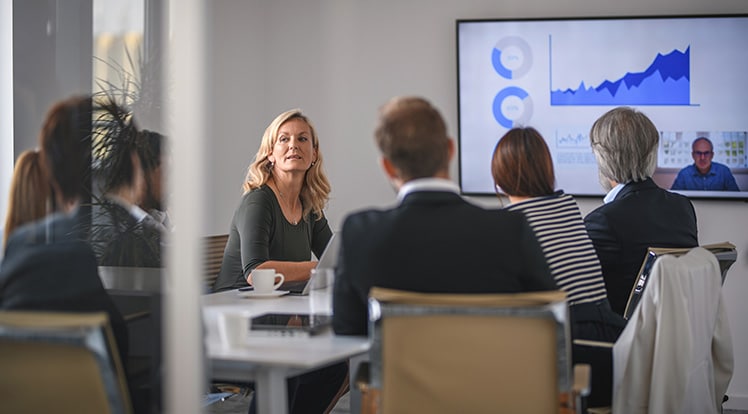
Management of construction risk means taking steps to minimize the chance of a project going wrong. Conducting a brainstorming session is the first step. This will help identify risks. Brainstorming sessions are not intended to resolve specific problems. Instead, they aim to identify possible scenarios during the project. These sessions allow the team to draw upon its collective knowledge and expertise to come up with possible solutions. A team can also look at past projects to determine risks.
Common causes of construction risks
Construction sites come with many dangers. Therefore, it is crucial to make sure that construction sites are managed safely. Managers should report any risks to the appropriate authorities and take necessary precautions to avoid them. Hazards include uneven surfaces, falling objects, and other hazards associated manual handling. Also, it is important to keep the job site clean and well lit. Also, any equipment or trailing cables should not be placed at a low location to minimize slipping and tripping hazards.
Another danger is change orders. These are an inevitable aspect of construction. These can create a lot more work if they are not properly managed. In some cases, change orders may even affect the overall success of the project. It is possible for a project to be delayed if subcontractors fail to communicate well. This could result in wasted materials or costly reworks.
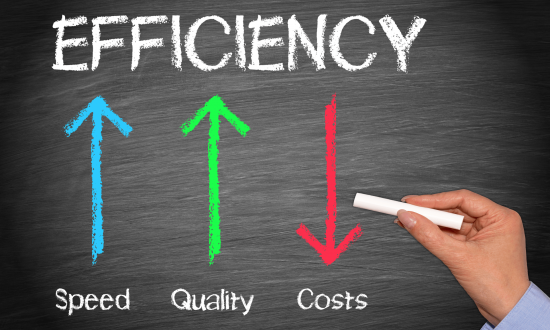
Mitigation strategies
The key part of project management is to create mitigation strategies. Project teams need to develop plans for managing and monitoring risk. They also need to evaluate these plans. These plans should take into consideration the unique nature of each project and its specific objectives. Project teams can minimize risk and protect their projects by implementing these strategies.
It is important to prioritize and identify risks according the likelihood and impact of them. Prioritizing high-impact risk areas should be done first and low-impact ones should be addressed later. For example, high-impact risks include materials price increases, which hurt margins. Inclement weather and geological phenomena, which can impact the project's success, are both low-impact and medium-risk.
Plan ahead
Preplanning to manage construction risk involves identifying the most significant risks early in the project. This will allow team members to identify and mitigate potential challenges as early as possible. It's a great opportunity for team members to share their expertise and perspectives. You may discover hidden risks that you hadn't considered. The process of risk identification should be ongoing, with meetings to discuss new risks as they arise.
Preplanning considers the entire construction process, beginning and ending. This process is designed to reduce loss and minimize disruptions while maximising efficiency. If done correctly, planning can reduce or eliminate certain risks.
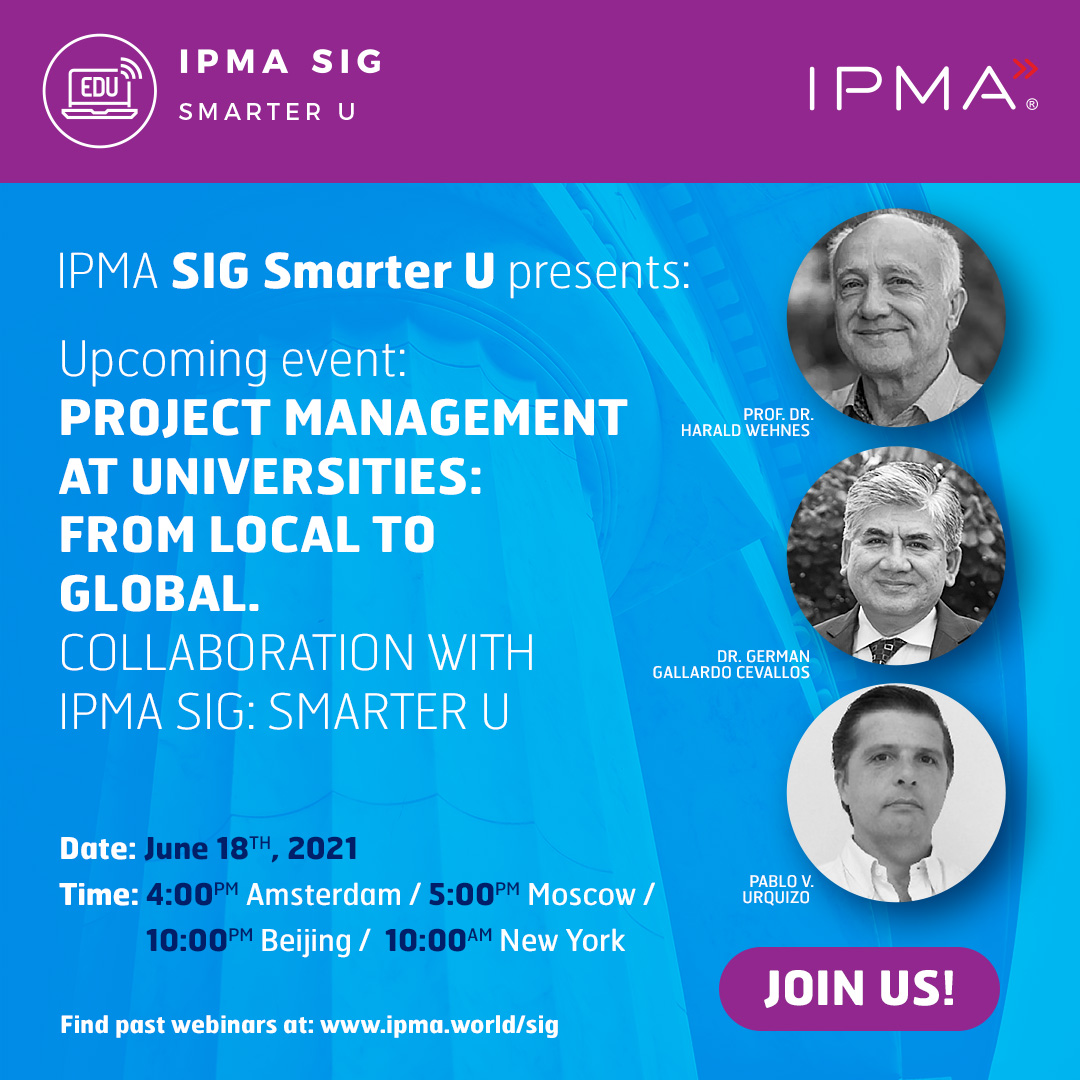
Transferring risk
Transferring construction risk can be a great way for contractor and owner to reduce their exposure in the event that there is an accident or a lawsuit. But it is essential to transfer risk effectively. You have many options to accomplish this, and it's important to start as soon as you can. Continue reading to learn more about risk transfer and how to make your program successful.
Good risk management strategies will help to allocate project risks to those who can control them best. The construction owner, typically a government agency, will generally assume the majority of the risk, and the contractor will transfer it to its suppliers and subcontractors.
FAQ
How do we create a company culture that is productive?
A culture of respect and value within a company is key to a productive culture.
It is founded on three basic principles:
-
Everyone has something to contribute
-
People are treated fairly
-
Respect is shared between individuals and groups
These values reflect in how people behave. For example, they will treat others with courtesy and consideration.
They will respect the opinions of others.
And they will encourage others to share ideas and feelings.
A company culture encourages collaboration and communication.
People feel safe to voice their opinions without fear of reprisal.
They understand that mistakes can be forgiven as long as they're dealt with honestly.
The company culture promotes honesty, integrity, and fairness.
Everyone knows that they must always tell truth.
Everyone understands that there are rules and regulations which apply to them.
Nobody expects to be treated differently or given favors.
What are the 4 main functions of management?
Management is responsible to plan, organize, direct, and control people and resources. It also includes developing policies and procedures and setting goals.
Management assists an organization in achieving its goals by providing direction, coordination and control, leadership, motivation, supervision and training, as well as evaluation.
Management's four main functions are:
Planning - Planning is about determining what must be done.
Organizing - Organization involves deciding what should be done.
Directing - Directing is when you get people to do what you ask.
Controlling: Controlling refers to making sure that people do what they are supposed to.
What is a fundamental management tool for decision-making?
A decision matrix, a simple yet powerful tool for managers to make decisions, is the best. They can think about all options and make informed decisions.
A decision matrix represents alternatives in rows and columns. This makes it easy for you to see how each option affects other options.
The boxes on the left hand side of this matrix represent four possible choices. Each box represents an option. The top row displays the current situation, and the bottom row shows what might happen if nothing is done.
The effect of Option 1 can be seen in the middle column. This would result in an increase of sales of $2 million to $3million.
These are the results of selecting Options 2 or 3. These are positive changes - they increase sales by $1 million and $500 thousand respectively. They also have negative consequences. Option 2 can increase costs by $100 million, while Option 3 can reduce profits by $200,000.
The last column displays the results of selecting Option 4. This involves decreasing sales by $1 million.
A decision matrix has the advantage that you don’t have to remember where numbers belong. You just look at the cells and know immediately whether any given a choice is better than another.
This is because the matrix has done all the hard work. It's simply a matter of comparing the numbers in the relevant cells.
Here's an example of how you might use a decision matrix in your business.
Decide whether you want to invest more in advertising. You'll be able increase your monthly revenue by $5000 if you do. However, this will mean that you'll have additional expenses of $10,000.
Look at the cell immediately below the one that states "Advertising" to calculate the net investment in advertising. It's $15,000. Advertising is worth much more than the investment cost.
Statistics
- As of 2020, personal bankers or tellers make an average of $32,620 per year, according to the BLS. (wgu.edu)
- Hire the top business lawyers and save up to 60% on legal fees (upcounsel.com)
- 100% of the courses are offered online, and no campus visits are required — a big time-saver for you. (online.uc.edu)
- The BLS says that financial services jobs like banking are expected to grow 4% by 2030, about as fast as the national average. (wgu.edu)
- Your choice in Step 5 may very likely be the same or similar to the alternative you placed at the top of your list at the end of Step 4. (umassd.edu)
External Links
How To
What is Lean Manufacturing?
Lean Manufacturing is a method to reduce waste and increase efficiency using structured methods. They were created by Toyota Motor Corporation in Japan in the 1980s. The aim was to produce better quality products at lower costs. Lean manufacturing eliminates unnecessary steps and activities from a production process. It includes five main elements: pull systems (continuous improvement), continuous improvement (just-in-time), kaizen (5S), and continuous change (continuous changes). It is a system that produces only the product the customer requests without additional work. Continuous improvement is the continuous improvement of existing processes. Just-in–time refers when components or materials are delivered immediately to their intended destination. Kaizen is continuous improvement. This can be achieved by making small, incremental changes every day. Fifth, the 5S stand for sort, set up in order to shine, standardize, maintain, and standardize. These five elements work together to produce the best results.
Lean Production System
Six key concepts are the basis of lean production:
-
Flow: The goal is to move material and information as close as possible from customers.
-
Value stream mapping is the ability to divide a process into smaller tasks, and then create a flowchart that shows the entire process.
-
Five S's – Sort, Put In Order Shine, Standardize and Sustain
-
Kanban is a visual system that uses visual cues like stickers, colored tape or stickers to keep track and monitor inventory.
-
Theory of constraints: Identify bottlenecks and use lean tools such as kanban boards to eliminate them.
-
Just-intime - Order components and materials at your location right on the spot.
-
Continuous improvement - incremental improvements are made to the process, not a complete overhaul.