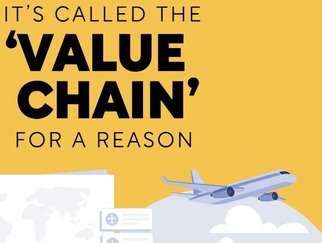
Manage involves taking decisions and directing tasks towards achieving a goal. This article will explain how to manage various tasks. It includes creating and maintaining an environment that encourages others to reach their goals. In an organization, managing involves getting things done with and through people informally organized into groups. Here are some tasks that most people deal with. These tasks are:
Management is the coordination or administration of tasks that lead to a goal.
The definition of management varies widely, depending on the organization, industry, and workplace. Management involves setting the strategy of an organization and coordinating the efforts of staff. It also includes staff seniority. Management also refers to the management and control of resources. Despite all the differences, there are certain common traits. These are examples of management roles.
It requires creating an internal environment
There are seven elements that influence the business environment. These include the value system of the organization, its mission, and objectives, the organizational structure, the style of top management, the quality of human resources, labour unions, and the physical resources of the organization. Beyond these, the firm's internal environment has a significant impact on its decision making. Creating a culture that fosters innovation and enables employees to make good decisions is crucial to an organization's success.
This involves convincing someone or something to achieve a desired result.
Persuasion is the process of persuading someone/something to do something. Although it can be difficult, in certain situations it is the right choice. Below are some tips to help persuade others. Try them!
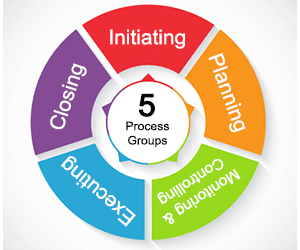
It involves getting things done with those informally organized groups
Management is the art and science of getting things done. Informally organized groups are the backbone for a business while formal organizations are its brains. The former allows a company to continue its standard production process, while formal organizations are there when an unexpected problem occurs. This theory is based in part on Harold Koontz, an American organizational thinker.
FAQ
Why is it so hard to make smart business decisions?
Complex business systems have many moving parts. They require people to manage multiple priorities and deal with uncertainty and complexity.
Understanding the impact of these factors on the system is crucial to making sound decisions.
You must first consider what each piece of the system does and why. Then, you need to think about how these pieces interact with one another.
You need to ask yourself if your previous actions have led you to make unfounded assumptions. If you don't have any, it may be time to revisit them.
For help, ask someone else if you're still stumped after all the above. They might see things differently than you and may have some insights that could help find a solution.
What are the steps of the management decision-making process?
The decision-making process of managers is complicated and multifaceted. It involves many elements, including analysis, strategy. planning. implementation. measurement. evaluation. feedback.
Management of people requires that you remember that they are just as human as you are, and can make mistakes. You are always capable of improving yourself, and there's always room for improvement.
This video will explain how decision-making works in Management. We discuss different types of decisions as well as why they are important and how managers can navigate them. The following topics will be covered:
How can we create a successful company culture?
A successful company culture is one that makes people feel valued and respected.
It is founded on three basic principles:
-
Everybody can contribute something valuable
-
People are treated fairly
-
There is mutual respect between individuals and groups
These values reflect in how people behave. For example, they will treat others with courtesy and consideration.
They will listen to other people's opinions respectfully.
These people will inspire others to share thoughts and feelings.
Additionally, the company culture encourages open communication as well as collaboration.
People feel free to express their views openly without fear of reprisal.
They know mistakes will be accepted as long as they are dealt with honestly.
The company culture encourages honesty and integrity.
Everyone knows that they must always tell the truth.
Everyone understands that there are rules and regulations which apply to them.
Everyone does not expect to receive special treatment.
What is the difference between project and program?
A program is permanent, whereas a project is temporary.
A project is usually defined by a clear goal and a set deadline.
It is usually done by a group that reports back to another person.
A program often has a set goals and objectives.
It is usually implemented by a single person.
What kind of people use Six Sigma
Six-sigma will be well-known to anyone who has worked in operations research or statistics. Anyone involved in business can benefit.
Because it requires a high degree of commitment, only leaders with strong leadership skills can implement it successfully.
What is Six Sigma and how can it help you?
It's an approach to quality improvement that emphasizes customer service and continuous learning. The goal is to eliminate defects by using statistical techniques.
Motorola developed Six Sigma in 1986 to help improve its manufacturing processes.
The idea spread quickly in the industry. Today many organizations use six-sigma techniques to improve product design.
What is the difference between leadership and management?
Leadership is about being a leader. Management is all about controlling others.
A leader inspires others while a manager directs them.
A leader inspires others to succeed, while a manager helps workers stay on task.
A leader develops people; a manager manages people.
Statistics
- This field is expected to grow about 7% by 2028, a bit faster than the national average for job growth. (wgu.edu)
- Our program is 100% engineered for your success. (online.uc.edu)
- 100% of the courses are offered online, and no campus visits are required — a big time-saver for you. (online.uc.edu)
- Your choice in Step 5 may very likely be the same or similar to the alternative you placed at the top of your list at the end of Step 4. (umassd.edu)
- The BLS says that financial services jobs like banking are expected to grow 4% by 2030, about as fast as the national average. (wgu.edu)
External Links
How To
How does Lean Manufacturing work?
Lean Manufacturing processes are used to reduce waste and improve efficiency through structured methods. They were created by Toyota Motor Corporation in Japan in the 1980s. The primary goal was to make products with lower costs and maintain high quality. Lean manufacturing is about eliminating redundant steps and activities from the manufacturing process. It includes five main elements: pull systems (continuous improvement), continuous improvement (just-in-time), kaizen (5S), and continuous change (continuous changes). Pull systems allow customers to get exactly what they want without having to do extra work. Continuous improvement is constantly improving upon existing processes. Just-intime refers the time components and materials arrive at the exact place where they are needed. Kaizen is continuous improvement. This can be achieved by making small, incremental changes every day. Last but not least, 5S is for sort. These five elements work together to produce the best results.
The Lean Production System
Six key concepts form the foundation of the lean production system:
-
Flow - The focus is on moving information and material as close as possible to customers.
-
Value stream mapping - break down each stage of a process into discrete tasks and create a flowchart of the entire process;
-
Five S's: Sort, Shine Standardize, Sustain, Set In Order, Shine and Shine
-
Kanban - visual cues such as stickers or colored tape can be used to track inventory.
-
Theory of constraints: identify bottlenecks in your process and eliminate them using lean tools, such as kanban board.
-
Just-intime - Order components and materials at your location right on the spot.
-
Continuous improvement - incremental improvements are made to the process, not a complete overhaul.