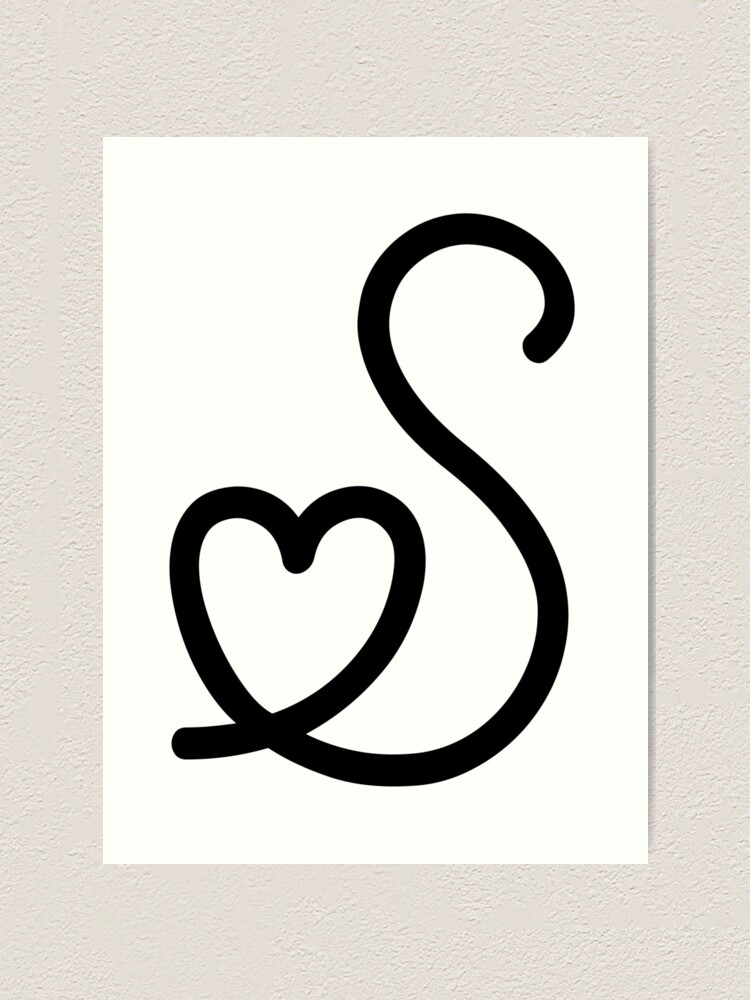
This book is a practical and strategic guide to managing global supply chain. Practitioners and researchers will find this book useful. It is comprehensive, clear and simple to read. Highly recommended. It covers the essential concepts and processes of strategic Supply Chain Management. They provide a step to follow approach for achieving strategic supplier chain goals. Both practitioners and researchers will find the book highly useful.
Demand-driven supply chains
A demand-driven supply chain is a strategic supply chain in which the entire chain responds to changes in demand. Companies can anticipate customer needs and respond to them in real-time. It differs from the traditional model, where the supplier announces the availability of a new product and the retailer takes delivery. This model allows companies to improve efficiency and control their inventories. Demand-driven supply chains allow companies to respond faster and more efficiently to customer needs.
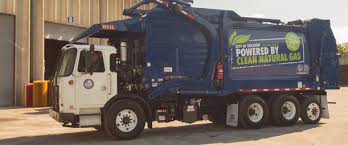
Planning
The supply chain planning and optimization tools used by organizations are organizational-based. The planning approaches differ in the extent of decision-making that they support. Successful companies should develop annual strategic business plans that identify potential growth opportunities. Many organizations use supply chain management software to optimize and plan their supply chains. Here are some examples of different planning approaches. You can pick one depending on which type of planning you prefer.
Execution
The formal management of a company's supply chain network is called strategic supply chain management. A supply chain manager creates a strategy that maximizes value, efficiency, resilience. It must align with the company's overarching business strategy. It takes careful planning and execution to manage your supply chain. Understanding your supply chain is key to your business strategy. Here are some ways to manage your supply chain effectively. Establish a vision for your supply chains.
Monitoring
Effective management depends on information. If a manager does not have the necessary data and tools to take action, their decisions will be ineffective. As supply chain complexity increases, managers who neglect to monitor it are not equipped to handle potential disruptions. Supply chain monitoring is crucial. There are many benefits to monitoring the supply chain. Here are just a few. Continue reading to learn how to get started.
Sustainability
It's difficult to ensure true sustainability in a supply chain. The more complex a supply chain, the harder it will be. A sustainability point person should be designated by the procurement team to oversee the sustainability process and assess the progress made by main suppliers. Also, the procurement team should set sustainability goals and make sure that suppliers achieve them. This way, the whole process will be transparent. The number of products and services that help the company achieve its sustainability goals is one way to measure supplier performance.
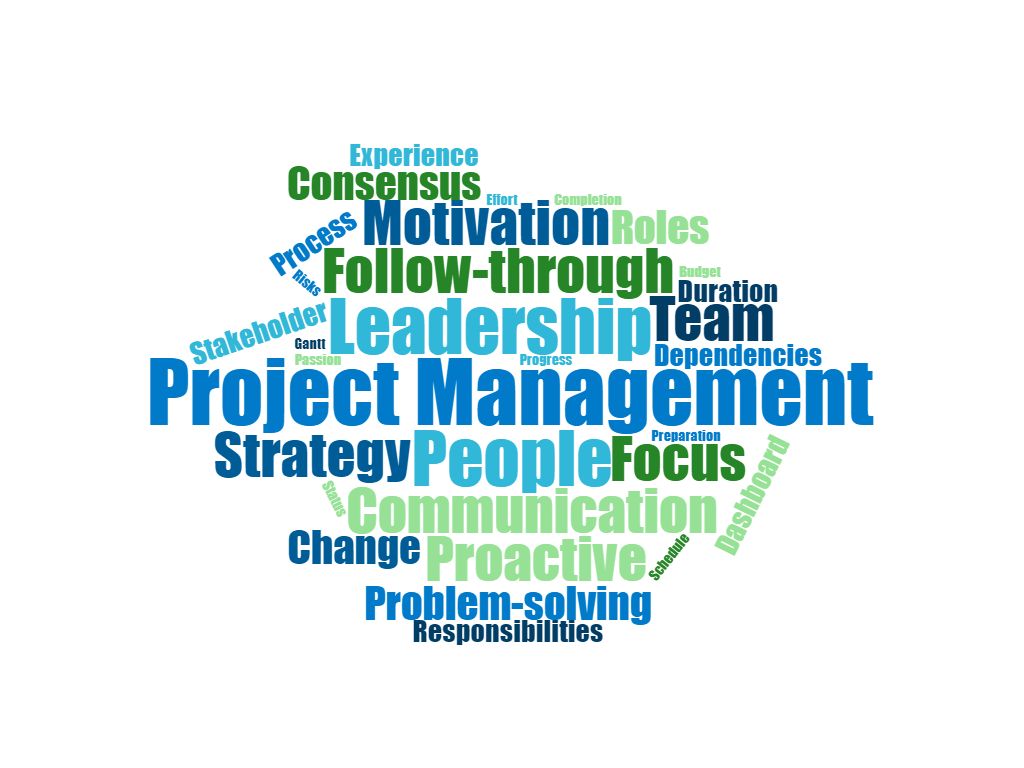
Variations according to product type
Companies should offer a broad range of products to consumers in order to maximize their performance. However, they often launch product variations without knowing whether they will add complexity to their supply chains. The number of new products launched by consumer-goods firms each year increased by 60 percent between 2002 and 2011. This influx of new products increased demand but also caused an increase in costs for their supply chains. For example, in the same period, U.S. consumer-goods companies increased the number of new products they introduced annually by 60 percent. Although this inevitably led to an increase in costs across many parts of the supply chain, it was steady at only 2.8 per year.
FAQ
Six Sigma is so well-known.
Six Sigma is simple to implement and can yield significant results. Six Sigma provides a framework to measure improvements and allows companies to focus on the most important things.
What are the steps involved in making a decision in management?
Managers are faced with complex and multifaceted decisions. It includes many factors such as analysis, strategy planning, implementation and measurement. Evaluation, feedback and feedback are just some of the other factors.
It is important to remember that people are human beings, just like you. They make mistakes. As such, there are always opportunities for improvement, especially when you put in the effort to improve yourself.
This video shows you how management makes decisions. We discuss different types of decisions as well as why they are important and how managers can navigate them. The following topics will be covered.
What kind of people use Six Sigma?
Six sigma is a common concept for people who have worked in statistics or operations research. It can be used by anyone in any business aspect.
Because it requires a high degree of commitment, only leaders with strong leadership skills can implement it successfully.
What is the role of a manager in a company?
Each industry has a different role for a manager.
A manager is generally responsible for overseeing the day to day operations of a company.
He/she ensures the company meets its financial commitments and produces goods/services that customers demand.
He/she ensures that employees follow the rules and regulations and adhere to quality standards.
He/she plans new products and services and oversees marketing campaigns.
Statistics
- Hire the top business lawyers and save up to 60% on legal fees (upcounsel.com)
- The BLS says that financial services jobs like banking are expected to grow 4% by 2030, about as fast as the national average. (wgu.edu)
- UpCounsel accepts only the top 5 percent of lawyers on its site. (upcounsel.com)
- The average salary for financial advisors in 2021 is around $60,000 per year, with the top 10% of the profession making more than $111,000 per year. (wgu.edu)
- This field is expected to grow about 7% by 2028, a bit faster than the national average for job growth. (wgu.edu)
External Links
How To
How can you implement a Quality Management Plan?
Quality Management Plan (QMP), which was introduced in ISO 9001:2008, provides a systematic approach to improving processes, products, and services through continual improvement. It helps to improve customer satisfaction and product/service quality by continuously measuring, analyzing, controlling and improving.
QMP is a common method to ensure business performance. QMP helps improve production, service delivery and customer relationships. QMPs should encompass all three components - Products and Services, as well as Processes. If the QMP only covers one aspect, it's called a "Process QMP". The QMP that focuses on a Product/Service is called a "Product." QMP. QMP is also used to refer to QMPs that focus on customer relations.
When implementing a QMP, there are two main elements: Scope and Strategy. These elements are as follows:
Scope: This is the scope of the QMP and its duration. For example, if you want to implement a QMP that lasts six months, then this scope will outline the activities done during the first six.
Strategy: These are the steps taken in order to reach the goals listed in the scope.
A typical QMP consists of 5 phases: Planning, Design, Development, Implementation, and Maintenance. Each phase is explained below:
Planning: This stage is where the QMP objectives are identified and prioritized. To understand the expectations and requirements of all stakeholders, the project is consulted. After identifying the objectives, priorities and stakeholder involvement, it's time to develop the strategy for achieving the goals.
Design: During this stage, the design team develops the vision, mission, strategies, and tactics required for the successful implementation of the QMP. These strategies are put into action by developing detailed plans and procedures.
Development: Here the development team works toward building the necessary resources and capabilities to support the successful implementation.
Implementation: This involves the actual implementation of the QMP using the planned strategies.
Maintenance: The maintenance of the QMP is an ongoing task.
Additionally, the QMP should include additional items:
Participation by Stakeholders is essential for the QMP's continued success. They should be involved in planning, design, development and implementation of the QMP.
Project Initiation: It is essential to have a clear understanding about the problem and the solution before you can initiate a project. This means that the initiator should know why they want something done and what they hope for from the end result.
Time Frame: This is a critical aspect of the QMP. The simplest version can be used if the QMP is only being implemented for a short time. If you're looking to implement the QMP over a longer period of time, you may need more detailed versions.
Cost Estimation. Cost estimation is another crucial component of QMP. Planning is not possible without knowing the amount of money you will spend. Cost estimation is crucial before you begin the QMP.
QMPs should not be considered a static document. It evolves as the company grows and changes. It should be reviewed on a regular basis to ensure that it is still meeting the company's needs.