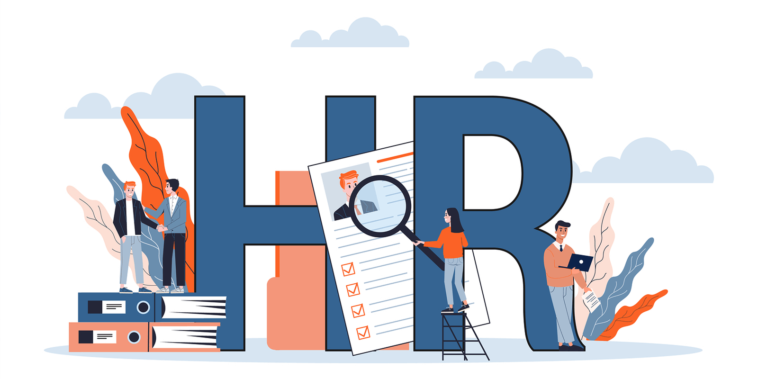
It is crucial to have effective change management training. It helps leaders lead their teams through the transition, educates employees and improves the success rates of an organization. In addition, effective change management training will increase the employee engagement, satisfaction, and productivity levels. Learn more by downloading our eBook: Change management training - 5 strategies to increase employee engagement and productivity
A strategic skill is effective change management training
Effective training sessions are a critical skill for change management. Although one-day, massive trainings may not be effective, smaller sessions that are asynchronous and combine live training with job tools and reference materials might prove more efficient. These flexible training methods enable organizations to be more responsive to changes. This article will help you to design training sessions that are relevant to your workforce.
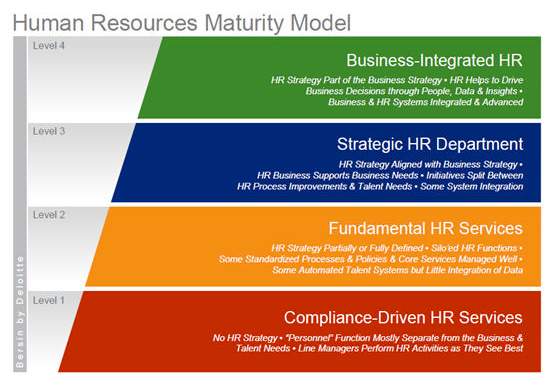
It allows leaders to guide their teams through changes
To be effective in managing change, you need both people and technical abilities. Along with technical skills, leaders must also be sensitive and understanding of the feelings of others. Communication must be both strategic and heartfelt. Leaders must show reassurance to employees who feel anxious or distrustful. Talking without taking action is likely to lead to distrust. The leader must be a role-model and act as one. Employees must also feel ownership for the changes.
It makes it easier for employees to grasp the significance of the change.
During a change management training, it is important to make sure that the changes employees are going to face are explained in detail. Change management training must make it easy for employees to grasp the changes and be useful in their job. This training must be repeated throughout training to ensure employees fully comprehend the changes. A formal statement stating the change should be provided during the training so that employees will be more familiar with it.
It is a way to increase your organization's success rates
This skill enables employees to adapt to change and perform their jobs. This training is often focused on a particular technology, organization structure, or overall strategy. The training program will vary depending on what organization it is. It is important to give employees a solid foundation for changing. Below are some essential steps to ensure your employees have the ability to manage change.
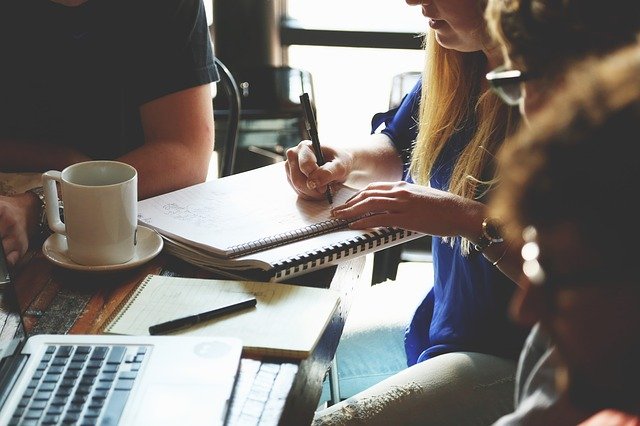
It prepares people to handle change.
The aim of change management training is to enable employees to accept, implement, and perform their jobs in conjunction with change. It helps employees understand the whys and hows of change and create better strategies for implementing them. By introducing change management training, individuals will become better champions for new products or services. This will increase their enthusiasm and help them adapt. They will also be more engaged. If they can manage change effectively, they will be able learn and apply the skills necessary to successfully lead and implement change initiatives.
FAQ
What is TQM and how can it help you?
The industrial revolution led to the birth and growth of the quality movement. Manufacturing companies realized they couldn't compete solely on price. They needed to improve the quality and efficiency of their products if they were to be competitive.
Management developed Total Quality Management to address the need for improvement. It focused on all aspects of an organisation's performance. It included continual improvement processes, employee involvement, customer satisfaction, and customer satisfaction.
What is the difference between TQM and Six Sigma?
The major difference between the two tools for quality management is that six Sigma focuses on eliminating defect while total quality control (TQM), on improving processes and decreasing costs.
Six Sigma is a methodology for continuous improvement. It emphasizes the elimination and improvement of defects using statistical methods, such as control charts, P-charts and Pareto analysis.
This method aims to reduce variation in product production. This is done by identifying and correcting the root causes of problems.
Total quality management is the measurement and monitoring of all aspects within an organization. It also involves training employees to improve performance.
It is often used as a strategy to increase productivity.
How to effectively manage employees
Effectively managing employees means making sure they are productive and happy.
This also involves setting clear expectations and monitoring their performance.
Managers need clear goals to be able to accomplish this.
They need to communicate clearly and openly with staff members. And they need to ensure that they reward good performance and discipline poor performers.
They also need to keep records of their team's activities. These include:
-
What was accomplished?
-
How much work was put in?
-
Who did it and why?
-
It was done!
-
Why?
This data can be used to evaluate and monitor performance.
How does Six Sigma work
Six Sigma uses statistics to measure problems, find root causes, fix them, and learn from past mistakes.
The first step is to identify the problem.
Next, data will be collected and analyzed to determine trends and patterns.
Next, corrective steps are taken to fix the problem.
Finally, data is reanalyzed to determine whether the problem has been eliminated.
This continues until the problem has been solved.
Statistics
- This field is expected to grow about 7% by 2028, a bit faster than the national average for job growth. (wgu.edu)
- Our program is 100% engineered for your success. (online.uc.edu)
- 100% of the courses are offered online, and no campus visits are required — a big time-saver for you. (online.uc.edu)
- As of 2020, personal bankers or tellers make an average of $32,620 per year, according to the BLS. (wgu.edu)
- Hire the top business lawyers and save up to 60% on legal fees (upcounsel.com)
External Links
How To
How do you do the Kaizen method?
Kaizen means continuous improvement. This Japanese term refers to the Japanese philosophy of continuous improvement that emphasizes incremental improvements and constant improvement. It is a process where people come together to improve their processes.
Kaizen is one of the most effective methods used in Lean Manufacturing. In this concept, employees who are responsible for the production line must identify problems that exist during the manufacturing process and try to solve them before they become big issues. This improves the quality of products, while reducing the cost.
Kaizen is an approach to making every worker aware and alert to what is happening around them. If something is wrong, it should be corrected immediately so that no problem occurs. So, if someone notices a problem while working, he/she should report it to his/her manager.
Kaizen follows a set of principles. When working with kaizen, we always start with the end result and move towards the beginning. For example, if we want to improve our factory, we first fix the machines that produce the final product. We then fix the machines producing components, and the machines producing raw materials. And finally, we fix the workers who work directly with those machines.
This is why it's called "kaizen" because it works step-by-step to improve everything. We finish fixing the factory and then go back to the beginning. This continues until we achieve perfection.
You need to know how to measure the effectiveness of kaizen within your business. There are several ways to determine whether kaizen is working well. One of these ways is to check the number of defects found on the finished products. Another way is determining how much productivity increased after implementing kaizen.
To determine if kaizen is effective, you should ask yourself why you chose to implement kaizen. Is it because the law required it or because you want to save money. It was a way to save money or help you succeed.
Suppose you answered yes to any of these questions, congratulations! You are now ready to begin kaizen.