
The management of supply chain risk involves various risks. These risks could be related either to the demand for a product or to the supply of raw material. Demand risks can occur when a business underestimates demand for a product. While supply risks can arise when raw material do not arrive on a timely basis. Both of these risks could cause disruptions to product flow. In the supply chain, there can be environmental risks due to social, political, or environmental issues.
Cybersecurity is a critical component of supply chain risk and management
Cybersecurity measures can be taken to safeguard critical assets. Supply chain risk management also includes cybersecurity measures. These measures can include the creation of a cybersecurity policy, and the establishment controls for suppliers. A contract should be drawn up by companies to detail their security requirements. These contracts should state what your suppliers are required to do to safeguard your assets. These contracts should outline what the supplier must do to protect your assets.
Cyber threats become more complex in the supply chain. They must be assessed and managed carefully. Cyber threats can affect any stage in the chain. They can cause serious damage to an organization's financial, brand, or operational health. Organizations must address cybersecurity concerns at every stage in the supply chain.
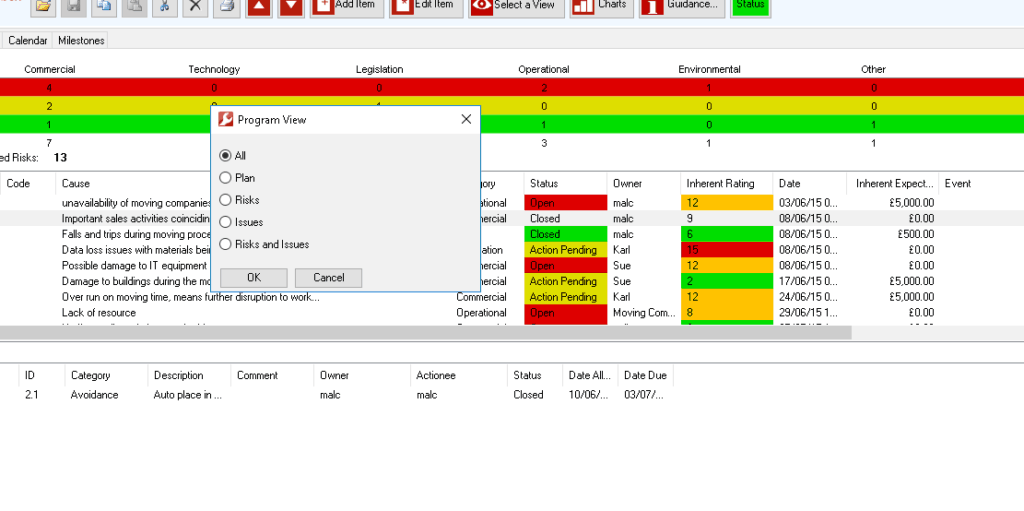
It requires a cross-functional team
Supply chain risk management requires a cross functional team to manage the risks associated with the entire supply chain. This strategy should include preparations, response, as well recovery. Preparation is about identifying high-risk areas, and developing contingency plans to deal with them. Prioritizing risks should be done according to their severity and likelihood. Visibility is also an important component of supply chain risk management strategies.
Executives have been slow to address the issue of supply chain risk management despite its importance. Respondents to a survey of 639 executives representing multiple industries and countries, 71% stated that their company was more exposed to supply-chain disruption than it was two years ago, and that 72 percent anticipated the risks will grow. Although several government agencies have been established to address supply chain risks, the private sector continues to search for a proven approach that will minimize business disruption.
Effective supply chain boards review the top risks in the supply chain and identify mitigation actions. Every participant becomes responsible for the mitigation action during the review. For example, a procurement representative will be responsible for onboarding and defining the qualifications of a new provider.
It requires technology
As organizations strive to reduce costs, increase resilience, many are rethinking their supply chain risk management strategies. They are turning to technology for better visibility and to manage risks before they occur. The right technology can help businesses build strong supply chains and create global networks. Companies need to have accurate data and visibility platforms in order to reap the full benefits of technology. These are essential for companies to effectively manage supply chain risk.
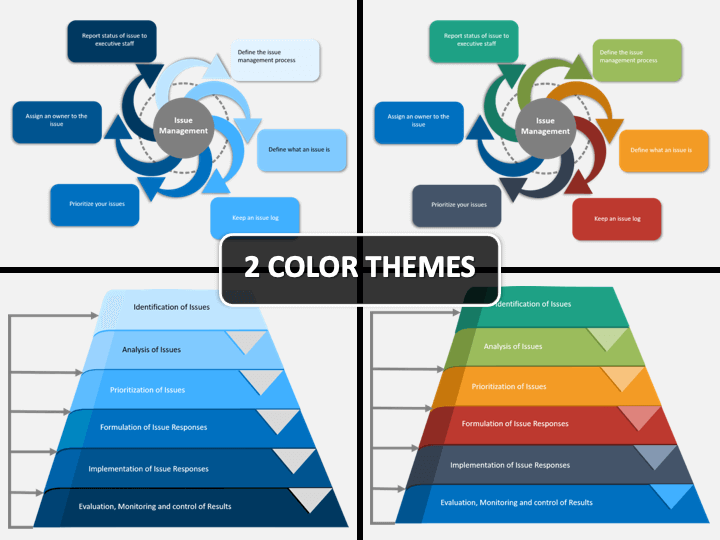
Supply chain risk management can be complex and multifaceted. Recent research of 639 industry executives revealed that 71% believed that their supply chains are more susceptible to disruption than they were in the past, and that this risk is expected to rise. In response, the United States government has launched a series of agencies to address supply chain risk, including the Protecting Critical Technology Task Force at the Department of Defense. Private companies are now looking for proven strategies that can help minimize the impact of supply chains risks on their business.
FAQ
What is TQM and how can it help you?
The quality movement was born during the industrial revolution when manufacturing companies realized they could not compete on price alone. They needed to improve quality and efficiency if they were going to remain competitive.
In response to this need for improvement, management developed Total Quality Management (TQM), which focused on improving all aspects of an organization's performance. It involved continuous improvement, employee participation, and customer satisfaction.
What are the most common errors made by managers?
Sometimes managers make it harder for their employees than is necessary.
They may not assign enough responsibilities to staff members and provide them with inadequate support.
Managers often lack the communication skills necessary to motivate and guide their teams.
Managers sometimes set unrealistic expectations of their teams.
Managers may attempt to solve all problems themselves, rather than delegating it to others.
What does Six Sigma mean?
Six Sigma uses statistical analyses to locate problems, measure them, analyze root cause, fix problems and learn from the experience.
First, identify the problem.
Next, data is collected and analyzed to identify trends and patterns.
Then, corrective actions can be taken to resolve the problem.
Finally, data is reanalyzed to determine whether the problem has been eliminated.
This continues until the problem has been solved.
What does it mean to say "project management"
This refers to managing all activities that are involved in a project's execution.
We help you define the scope of your project, identify the requirements, prepare the budget, organize the team, plan the work, monitor progress and evaluate the results before closing down the project.
What is the difference between a project and a program?
A project is temporary while a programme is permanent.
A project is usually defined by a clear goal and a set deadline.
It is often carried out by a team of people who report back to someone else.
A program is usually defined by a set or goals.
It is usually implemented by a single person.
Why is project management important for companies?
Project management techniques can be used to ensure smooth project execution and meeting deadlines.
This is due to the fact that most businesses rely heavily upon project work in order to produce goods, and services.
These projects are essential for companies.
Companies could lose their time, reputation, and money without effective project management.
How can a manager motivate employees?
Motivation refers to the desire or need to succeed.
Enjoyable activities can motivate you.
You can also get motivated by seeing your contribution to the success or the improvement of the organization.
You might find it more rewarding to treat patients than to study medical books if you plan to become a doctor.
A different type of motivation comes directly from the inside.
Perhaps you have a strong sense to give back, for example.
Or you might enjoy working hard.
Ask yourself why you feel so motivated.
Then try to think about ways to change your situation to be more motivated.
Statistics
- Our program is 100% engineered for your success. (online.uc.edu)
- The profession is expected to grow 7% by 2028, a bit faster than the national average. (wgu.edu)
- Your choice in Step 5 may very likely be the same or similar to the alternative you placed at the top of your list at the end of Step 4. (umassd.edu)
- Hire the top business lawyers and save up to 60% on legal fees (upcounsel.com)
- UpCounsel accepts only the top 5 percent of lawyers on its site. (upcounsel.com)
External Links
How To
How does Lean Manufacturing work?
Lean Manufacturing uses structured methods to reduce waste, increase efficiency and reduce waste. They were developed by Toyota Motor Corporation in Japan during the 1980s. The aim was to produce better quality products at lower costs. Lean manufacturing is about eliminating redundant steps and activities from the manufacturing process. It has five components: continuous improvement and pull systems; just-in time; continuous change; and kaizen (continuous innovation). It is a system that produces only the product the customer requests without additional work. Continuous improvement is the continuous improvement of existing processes. Just-in time refers to components and materials being delivered right at the place they are needed. Kaizen is continuous improvement. This can be achieved by making small, incremental changes every day. Finally, 5S stands for sort, set in order, shine, standardize, and sustain. These five elements work together to produce the best results.
Lean Production System
The lean production system is based on six key concepts:
-
Flow - focus on moving material and information as close to customers as possible;
-
Value stream mapping - Break down each stage in a process into distinct tasks and create an overview of the whole process.
-
Five S’s - Sorted, In Order. Shine. Standardize. And Sustain.
-
Kanban – visual signals like colored tape, stickers or other visual cues are used to keep track inventory.
-
Theory of constraints: identify bottlenecks in your process and eliminate them using lean tools, such as kanban board.
-
Just-intime - Order components and materials at your location right on the spot.
-
Continuous improvement: Make incremental improvements to the process instead of overhauling it completely.