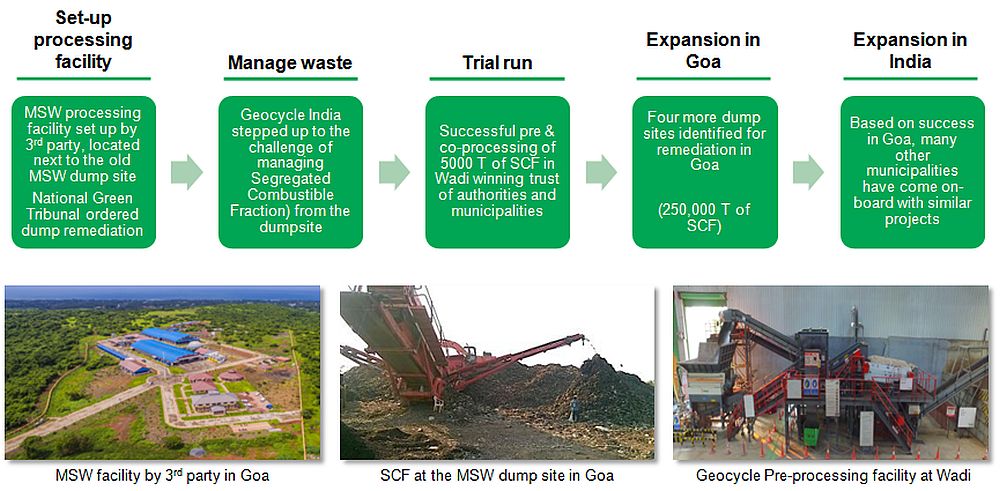
Construction contract laws vary from country to country. Although there are some universal principles, the laws on construction contracts can differ from one country to another. Different countries use different methods to resolve disputes. Get legal advice to ensure the law is applicable to your case. There are many ways to resolve disputes relating to construction contracts.
German construction law
German construction law has recently been updated, which could have implications on the practical implementation and application of standard business terms for construction projects. While the FIDIC Silver Book 2017 is based on the 1999 edition, there has been much debate about whether or not it is compatible with German law, which codifies standard business terms in section 305 of the BGB. This law is mandatory, and it is enforced through state courts.
A number of problems can arise for the construction principal if defects are found during construction. He may choose to continue construction but he must identify and prove the defects. Delays can also lead to the expiration of warranty claims. If this happens, the principal might face German construction court proceedings and financial loss.
Conditions for claiming damages resulting from delay in construction
Conditions for claiming damages due to delay in a construction project should be clear and precise. A construction contract will typically list items that could be delayed and the reasons for the delay. Notifying the other party in privity of any delay is important. Moreover, the contractor should seek to apportion the overall delay between the items.
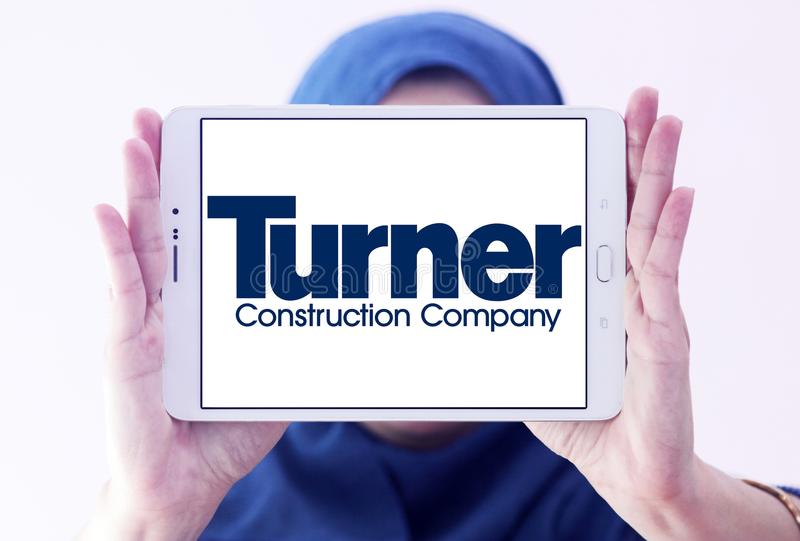
In order to determine if a delay resulted from a breach of a condition, the courts use a reasonable anticipation test. For example, an owner may know that a major piece of equipment will not be delivered by a contract deadline. To reduce this risk, an owner might insert a clause that provides for a delay of 60 days and a reasonable extension. Contractors who violate this clause will not be able to claim damages for any delay.
The architect's liability
A plan or design that isn't in compliance with the requirements of construction law or its specifications becomes a liability for an architect. An architect cannot escape liability for unsafe designs or other defects by claiming that he obtained permission from his employer. In these cases, the architect will need to prove that they did not breach material duty.
When determining liability for an architect, there are many factors to take into account. First, the architect should have undertaken all the relevant investigations. If the architect fails to complete these investigations, the client may sue him for negligence in order to receive compensation for any damages.
Subcontractor's liability
In a construction lawsuit, the liability of a subcontractor may arise. If work was not upheld, a subcontractor might be held responsible for a defect in construction. This is similar to the contractor owner liability doctrine. For subcontractor liability to apply, the subcontractor must either have reasonably expected to have known or have knowledge of the defect.
Indemnity clauses are an integral part of construction law. They can reduce a subcontractor's liability if the other party is held liable. Indemnity agreements are often signed between contractors and subcontractors. These agreements protect each party from liability for problems that might arise during construction. Indemnity agreements can be used to limit liability and protect both the parties.
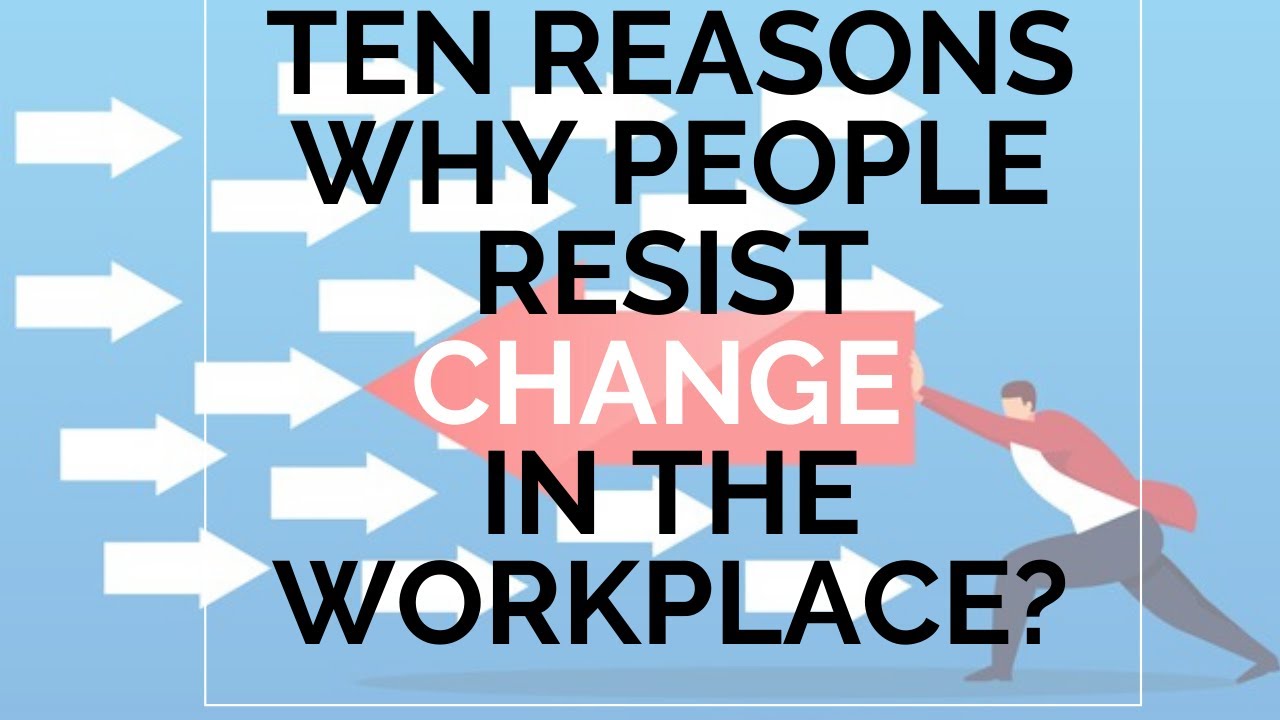
Liability of the owner
The nature of the defect is a factor that determines whether the owner is liable under construction law. In most cases, the owner is not liable for the construction of the defect. The contractor must complete the project according the plans and specifications. In some cases, however the owner may be responsible for the defect. A contractor may have been misled by the owner about the location of the building, which could lead to the structure's failure.
A construction defect may also occur due to a defective product. Subcontractors can also file a claim against an owner for economic damages if the owner fails in their job. This can be done by filing a Uniform Civil Code claim against manufacturer.
FAQ
Six Sigma is so popular.
Six Sigma is easy to implement and can produce significant results. Six Sigma provides a framework to measure improvements and allows companies to focus on the most important things.
It can sometimes seem difficult to make business decisions.
Businesses are complex systems, and they have many moving parts. They require people to manage multiple priorities and deal with uncertainty and complexity.
It is important to understand the effects of these factors on the system in order to make informed decisions.
You must first consider what each piece of the system does and why. Next, consider how each piece interacts with the others.
Also, you should ask yourself if there have been any assumptions in your past behavior. You might consider revisiting them if they are not.
If you're still stuck after all this, try asking someone else for help. You may be able to see things from a different perspective than you are and gain insight that can help you find a solution.
What is the main difference between Six Sigma Six Sigma TQM and Six Sigma Six Sigma?
The major difference between the two tools for quality management is that six Sigma focuses on eliminating defect while total quality control (TQM), on improving processes and decreasing costs.
Six Sigma is an approach for continuous improvement. This approach emphasizes eliminating defects through statistical methods like control charts, Pareto analysis, and p-charts.
This method attempts to reduce variations in product output. This is achieved by identifying and addressing the root causes of problems.
Total quality management includes monitoring and measuring all aspects of an organization's performance. It also involves training employees to improve performance.
It is commonly used as a strategy for increasing productivity.
How can we create a culture of success in our company?
Successful company culture is one where people feel valued and respected.
It is founded on three basic principles:
-
Everybody can contribute something valuable
-
People are treated fairly
-
It is possible to have mutual respect between groups and individuals
These values reflect in how people behave. They will treat others with kindness and consideration.
They will be respectful of the opinions of other people.
They encourage others to express their feelings and ideas.
In addition, the company culture encourages open communication and collaboration.
People are free to speak out without fear of reprisal.
They understand that errors will be tolerated as long they are corrected honestly.
Finally, the company culture promotes honesty and integrity.
Everyone is aware that truth must be told.
Everyone understands that there are rules and regulations which apply to them.
Nobody expects to be treated differently or given favors.
Statistics
- This field is expected to grow about 7% by 2028, a bit faster than the national average for job growth. (wgu.edu)
- As of 2020, personal bankers or tellers make an average of $32,620 per year, according to the BLS. (wgu.edu)
- Our program is 100% engineered for your success. (online.uc.edu)
- UpCounsel accepts only the top 5 percent of lawyers on its site. (upcounsel.com)
- The BLS says that financial services jobs like banking are expected to grow 4% by 2030, about as fast as the national average. (wgu.edu)
External Links
How To
How do you implement Quality Management Plans (QMPs)?
QMP (Quality Management Plan) is a system to improve products and services by implementing continuous improvement. It is about how to continually measure, analyze, control, improve, and maintain customer satisfaction.
QMP is a standard way to improve business performance. QMP helps improve production, service delivery and customer relationships. A QMP should include all three aspects - Processes, Products, and Services. A "Process" QMP is one that only includes one aspect. If the QMP is focused on a product/service, it's called a QMP. QMP is also used to refer to QMPs that focus on customer relations.
There are two key elements to implementing a QMP: Strategy and Scope. They are defined as follows:
Scope: This describes the scope and duration for the QMP. This will be used to define activities that are performed in the first six months of a QMP.
Strategy: This describes how you will achieve the goals in your scope.
A typical QMP consists of 5 phases: Planning, Design, Development, Implementation, and Maintenance. Below is a description of each phase:
Planning: In this stage the QMP's objectives and priorities are established. In order to fully understand and meet the needs of all stakeholders involved in this project, they are consulted. Next, you will need to identify the objectives and priorities. The strategy for achieving them is developed.
Design: In this stage, the design team designs the vision and mission, strategies, as well as the tactics that will be required to successfully implement the QMP. These strategies are then put into practice by creating detailed plans.
Development: The development team is responsible for building the resources and capabilities necessary to implement the QMP effectively.
Implementation: This is the actual implementation and use of the QMP's planned strategies.
Maintenance: It is an ongoing process that maintains the QMP over time.
The QMP must also include several other items:
Participation of Stakeholders: The QMP's success depends on the participation of stakeholders. They are required to actively participate in the planning, design and development of the QMP, as well as the implementation and maintenance phases.
Initiation of a Project: A clear understanding and application of the problem statement is crucial for initiating a project. The initiator must know the reason they are doing something and the expected outcome.
Time Frame: It is important to consider the QMP's time frame. A simple version is fine if you only plan to use the QMP for a brief period. However, if you have a long-term commitment, you may require more elaborate versions.
Cost Estimation is another important aspect of the QMP. It is impossible to plan without knowing what you will spend. It is therefore important to calculate the cost before you start the QMP.
QMPs are not only a document, but also a living document. This is the most important aspect of QMPs. It is constantly changing as the company changes. So, it should be reviewed periodically to make sure that it still meets the needs of the organization.