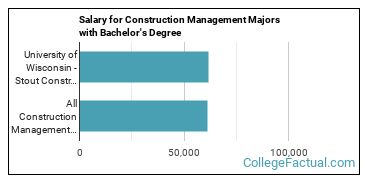
Your business can reduce risk by using a good risk asset management program. This system helps you identify which processes and assets are most at risk. It is possible to make informed decisions about how to implement an effective strategy by analyzing the risks and determining what the consequences may be.
Any business needs a risk management system. A lack of risk management can lead to unfounded risks for your company or even disciplinary action. You can determine how much risk you are willing and then put in place a system to reduce that risk.
Risk asset management is essential for ensuring the safety of your staff, your company, and the environment. A risk asset management program should be able monitoring and tracking your company's assets and providing an accurate report on the risks. It helps you to identify the risks unique to your company.
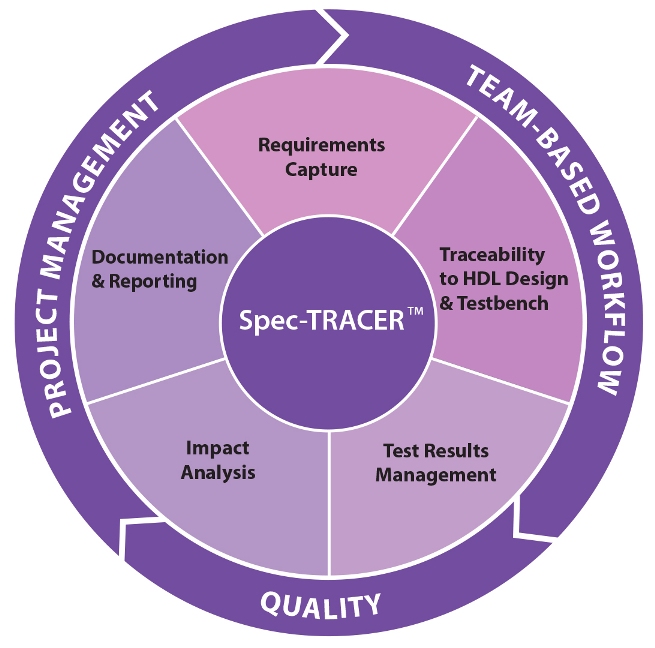
BEC attacks should be detected by risk asset management systems. This type can lead to data breach and ransomware attack. These attacks are very common in many industries. BEC attacks are an example of industrial spying. Threat actors request ransoms from companies to access time-sensitive information.
The road-map should be included in a risk asset management system. This plan describes how your organization will implement risk mitigation techniques in order to provide satisfactory levels of service. The roadmap is critical to ensure that the infrastructure assets used are properly managed in order to maximize their service life.
You should also have the ability to generate accurate reports from your asset risk management software. An EAM system is a comprehensive platform that can be used to produce reports on asset performance as well maintenance and risk management. It allows you to prioritize your asset investments on the basis of criticality and asset lifecycle.
E&R has been increasingly concerned with risk management. This industry faces numerous environmental challenges and is responsible for aging assets. It must also comply with regulatory compliance requirements. It is also under constant pressure to lower costs and perform better. In order to maintain the industry's competitive edge, the E&R industry must continually seek ways to improve its performance.
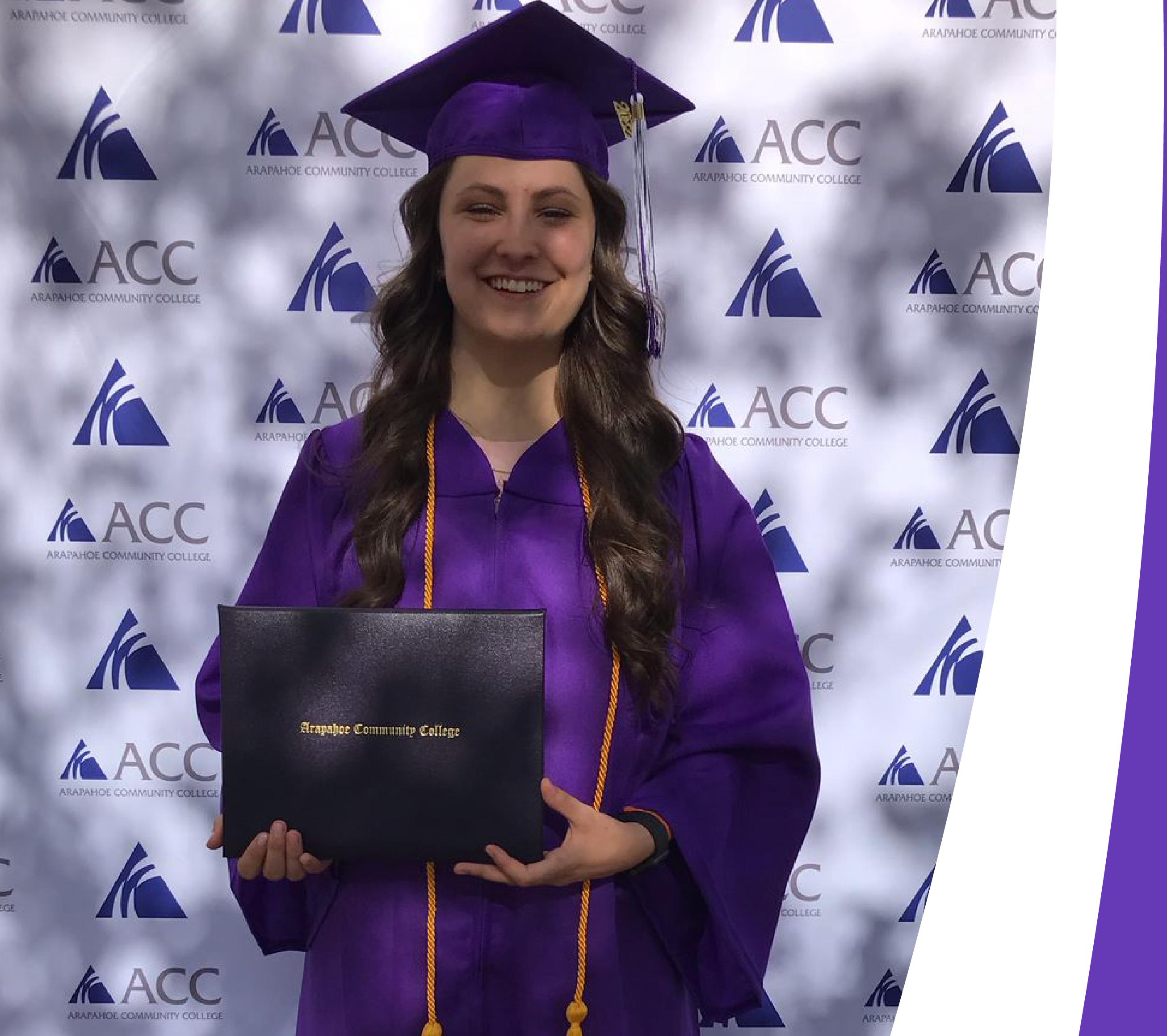
Improved asset management is one of the best ways for your company to perform better. You can increase the value of your assets by improving their performance. This process involves assessing the risks of assets, identifying those that may impact your operations, and implementing strategies to mitigate those risks. Although this is a complicated process, it is essential for all organizations.
Asset management may include managing client portfolios and managing uncertainty. Asset managers are fiduciary and responsible for making ethical and legal decisions on behalf clients.
FAQ
What is the difference of leadership and management?
Leadership is about inspiring others. Management is all about controlling others.
Leaders inspire followers, while managers direct workers.
A leader motivates people to achieve success; a manager keeps workers on task.
A leader develops people; a manager manages people.
Which kind of people use Six Sigma
Six sigma is a common concept for people who have worked in statistics or operations research. Anybody involved in any aspect or business can benefit.
Because it requires a high degree of commitment, only leaders with strong leadership skills can implement it successfully.
What do we mean when we say "project management"?
It refers to the management of activities related to a project.
This includes defining the scope, identifying the requirements and preparing the budget. We also organize the project team, schedule the work, monitor progress, evaluate results, and close the project.
Statistics
- The BLS says that financial services jobs like banking are expected to grow 4% by 2030, about as fast as the national average. (wgu.edu)
- Your choice in Step 5 may very likely be the same or similar to the alternative you placed at the top of your list at the end of Step 4. (umassd.edu)
- The profession is expected to grow 7% by 2028, a bit faster than the national average. (wgu.edu)
- 100% of the courses are offered online, and no campus visits are required — a big time-saver for you. (online.uc.edu)
- Hire the top business lawyers and save up to 60% on legal fees (upcounsel.com)
External Links
How To
How is Lean Manufacturing done?
Lean Manufacturing methods are used to reduce waste through structured processes. They were created in Japan by Toyota Motor Corporation during the 1980s. The primary goal was to make products with lower costs and maintain high quality. Lean manufacturing is about eliminating redundant steps and activities from the manufacturing process. It has five components: continuous improvement and pull systems; just-in time; continuous change; and kaizen (continuous innovation). It is a system that produces only the product the customer requests without additional work. Continuous improvement is the continuous improvement of existing processes. Just-intime refers the time components and materials arrive at the exact place where they are needed. Kaizen means continuous improvement. Kaizen involves making small changes and improving continuously. Five-S stands for sort. It is also the acronym for shine, standardize (standardize), and sustain. These five elements are combined to give you the best possible results.
The Lean Production System
Six key concepts are the basis of lean production:
-
Flow is about moving material and information as near as customers can.
-
Value stream mapping - Break down each stage in a process into distinct tasks and create an overview of the whole process.
-
Five S's: Sort, Shine Standardize, Sustain, Set In Order, Shine and Shine
-
Kanban - visual cues such as stickers or colored tape can be used to track inventory.
-
Theory of Constraints - Identify bottlenecks in the process, and eliminate them using lean tools such kanban boards.
-
Just-in-time delivery - Deliver components and materials right to your point of use.
-
Continuous improvement - make incremental improvements to the process rather than overhauling it all at once.