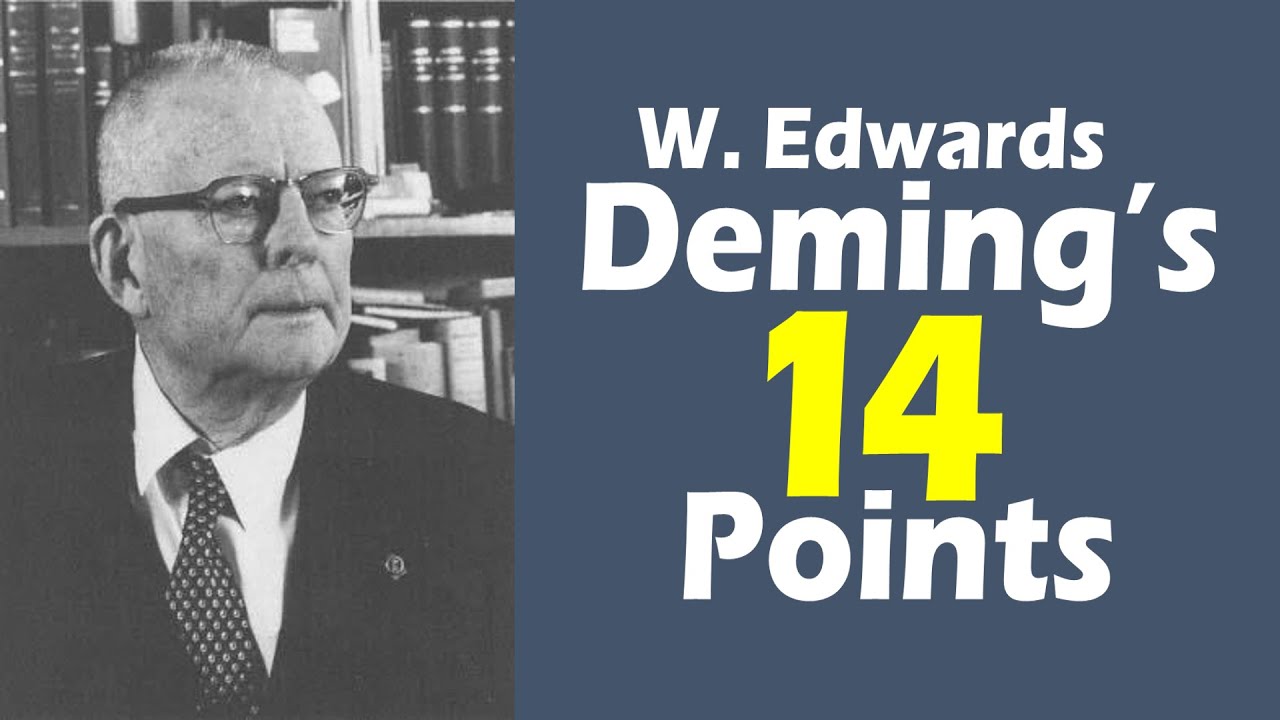
The certificate program in construction management can help you to be a leader within the field. Its cutting-edge curriculum provides students with a variety of essential skills that are vital in today's fast-paced industry. Learn about BIM, construction scheduling, green building and other topics. The program will also help them build strong leadership and interpersonal skills. A certificate in construction management is the best way for you to get started, regardless of whether your goal is to open your own company or work in the construction industry.
Coursework
This course is intended to improve the skills of construction managers. This course covers topics like project planning, scheduling and budgeting, as well as code compliance. Additionally, topics such as scheduling tools and the critical path methodology are covered. A student will also learn about cash flow diagrams. This course is necessary if one wants to work in construction.
To earn a construction management certificate at the U of M, a student must complete all coursework within four years of admission. The minimum GPA required to earn a construction management certificate at the University of Michigan is 2.00 or a C. The certificate can be awarded concurrently to an undergraduate degree. This program is intended for people with previous experience working in the construction industry. However, the student must be admitted to the program as early as possible.
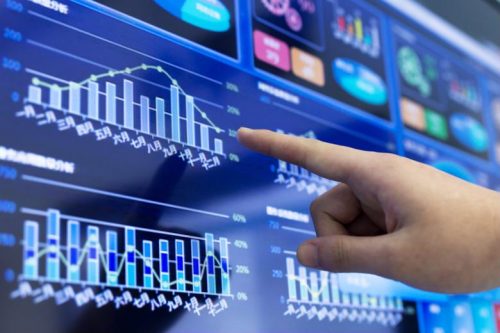
Credentials
A certificate in construction management is an important credential that you can have if you want to work in construction. It shows potential employers that this certification is something you care about. It can also give you a professional edge if you are interested in starting your own business or working as a freelancer. Different colleges and universities can offer credentials for construction management certificates. The construction industry is constantly changing and the skills you have to be successful are highly sought after.
Everyone involved in construction benefits from construction certifications. These programs elevate individual professional practices, the brand of a construction firm, and the quality of the services provided by workers. They show that a worker has a high level of skill and is knowledgeable about the construction industry. You can get a better rate for your services by obtaining this certification. Construction certifications are a great way to stand out among the crowd in many cities.
Requirements
Earning a construction management certificate may not necessarily lead to employment, but it can boost your job prospects. Typically, students who complete a certificate program gain knowledge in project delivery, building information modeling, and decision-making. The certificate programs last for two years and don't require any additional coursework. A certificate program can help you develop your professional skills by allowing you to demonstrate your knowledge in your field. However, it does not necessarily mean that you must be an expert in your industry to get a certificate.
Another option is to get an exam-style certification. This certificate can be purchased for $500 to $1,100. The cost of the certificate is payable once you pass the exam. You will need to meet certain requirements in order to earn a certificate. This depends on your education and background. It is worth taking the time to explore all of the options before you make a decision.
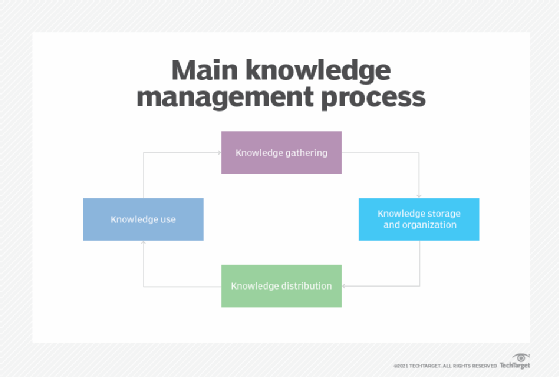
Online programs
Online construction management certificates are a great way for you to stand out from the rest of your job applicants. Employers will be able to see that you can take on a top-level position in a construction company by earning this certificate. Ashworth College offers competitive tuition rates for online construction management certificates. Click the links below for more information about this program. We hope you find this information useful. The construction industry is highly competitive, so earning your construction management certificate online will help you land that job.
You can earn a certificate in construction management to be more efficient in managing employees and coordination of projects. The course offers cutting-edge training in project management, scheduling BIM, construction law, green building, and other related topics. The course also emphasizes leadership and interpersonal skills. This is a great option for those who want to break into the construction industry, but don't have the time or education to pursue an advanced degree.
FAQ
How does a manager motivate their employees?
Motivation is the desire for success.
It is possible to be motivated by doing something you enjoy.
You can also feel motivated by making a positive contribution to the success in the organization.
For example: If you want to be a doctor, you might find it more motivating seeing patients than reading medical books all day.
Motivation comes from within.
You might feel a strong sense for responsibility and want to help others.
Or you might enjoy working hard.
Ask yourself why you feel so motivated.
Then try to think about ways to change your situation to be more motivated.
Why does it sometimes seem so difficult to make good business decisions?
Complex business systems have many moving parts. People who manage them have to balance multiple priorities while dealing with complexity and uncertainty.
It is important to understand the effects of these factors on the system in order to make informed decisions.
It is important to consider the functions and reasons for each part of the system. Next, consider how each piece interacts with the others.
You need to ask yourself if your previous actions have led you to make unfounded assumptions. You might consider revisiting them if they are not.
For help, ask someone else if you're still stumped after all the above. They might have different perspectives than you, and could offer insight that could help you solve your problem.
What do we mean when we say "project management"?
This refers to managing all activities that are involved in a project's execution.
We help you define the scope of your project, identify the requirements, prepare the budget, organize the team, plan the work, monitor progress and evaluate the results before closing down the project.
What is TQM, exactly?
The quality movement was born during the industrial revolution when manufacturing companies realized they could not compete on price alone. If they wanted to stay competitive, they needed to improve their quality and efficiency.
Management responded to the need to improve, and developed Total Quality Management (TQM). This focused on improving every aspect of an organization’s performance. It involved continuous improvement, employee participation, and customer satisfaction.
What is Six Sigma?
It is a way to improve quality that places emphasis on customer service and continuous learning. The objective is to eliminate all defects through statistical methods.
Motorola created Six Sigma as part of their efforts to improve manufacturing processes in 1986.
The idea spread quickly in the industry. Today many organizations use six-sigma techniques to improve product design.
What kind of people use Six Sigma?
Six Sigma will most likely be familiar to people who have worked in statistics and operations research. But anyone can benefit from it.
It requires high levels of commitment and leadership skills to be successful.
Statistics
- Our program is 100% engineered for your success. (online.uc.edu)
- Your choice in Step 5 may very likely be the same or similar to the alternative you placed at the top of your list at the end of Step 4. (umassd.edu)
- UpCounsel accepts only the top 5 percent of lawyers on its site. (upcounsel.com)
- 100% of the courses are offered online, and no campus visits are required — a big time-saver for you. (online.uc.edu)
- The BLS says that financial services jobs like banking are expected to grow 4% by 2030, about as fast as the national average. (wgu.edu)
External Links
How To
How does Lean Manufacturing work?
Lean Manufacturing processes are used to reduce waste and improve efficiency through structured methods. These processes were created by Toyota Motor Corporation, Japan in the 1980s. The main goal was to produce products at lower costs while maintaining quality. Lean manufacturing is about eliminating redundant steps and activities from the manufacturing process. It is composed of five fundamental elements: continuous improvement; pull systems, continuous improvements, just-in–time, kaizen, continuous change, and 5S. It is a system that produces only the product the customer requests without additional work. Continuous improvement is the continuous improvement of existing processes. Just-intime refers the time components and materials arrive at the exact place where they are needed. Kaizen means continuous improvement. Kaizen involves making small changes and improving continuously. Finally, 5S stands for sort, set in order, shine, standardize, and sustain. These five elements are combined to give you the best possible results.
Lean Production System
Six key concepts underlie the lean production system.
-
Flow is about moving material and information as near as customers can.
-
Value stream mapping is the ability to divide a process into smaller tasks, and then create a flowchart that shows the entire process.
-
Five S's - Sort, Set In Order, Shine, Standardize, and Sustain;
-
Kanban – visual signals like colored tape, stickers or other visual cues are used to keep track inventory.
-
Theory of constraints: Identify bottlenecks and use lean tools such as kanban boards to eliminate them.
-
Just-in-time delivery - Deliver components and materials right to your point of use.
-
Continuous improvement is making incremental improvements to your process, rather than trying to overhaul it all at once.