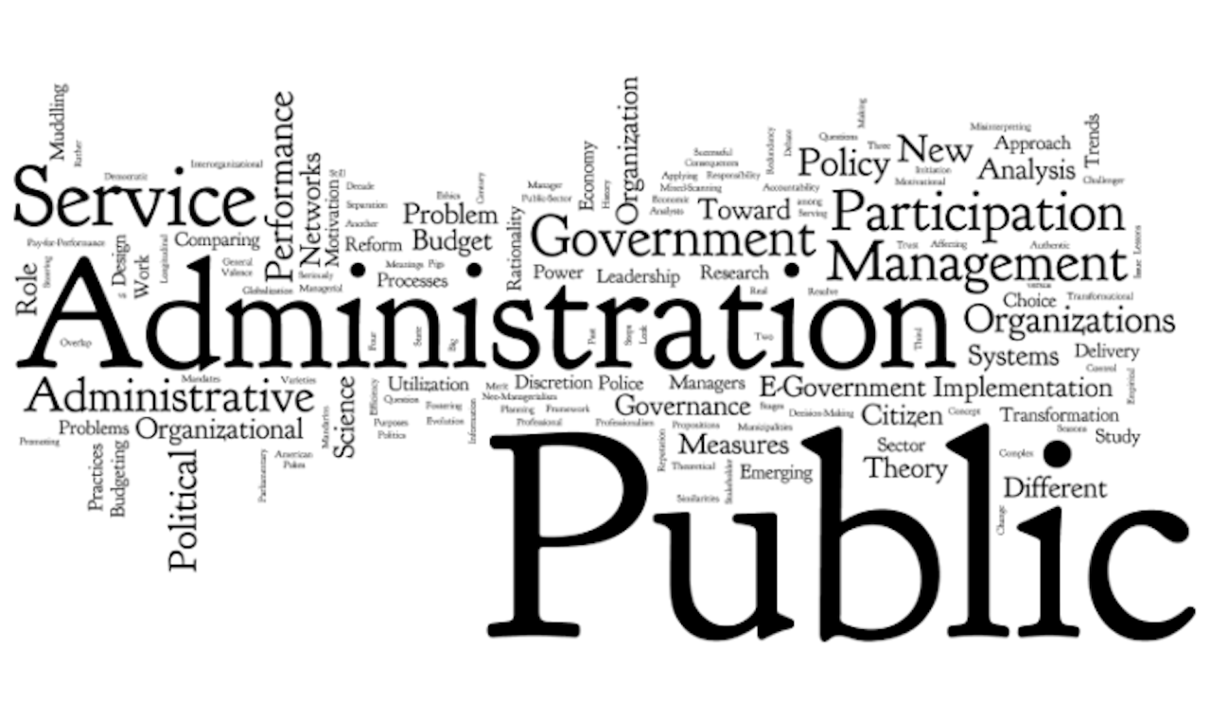
The Waste Management specialist is responsible for the development of project schedules as well as making service recommendations. The National Account Manager and this position help to build client relationships as well as new program initiatives. The Waste Management Specialist works as a team member and recruits associates to attain professional standards. They also coordinate with the National Account Manager to ensure that clients are getting the best possible service from the company. Additionally, the position supervises and leads projects.
Jim Bentley
Advanced Disposal National Accounts, a complete waste management company, is the commercial division. Jim Bentley will develop relationships with potential clients, clients, and strategic partner vendors. He will also manage business development with other companies within the company's vast network of over 7,000 environmental service providers throughout North America. Bentley has 21 years of solid waste experience, including a stint as a senior account executive at Green Leaf Compaction.
Ashish Sharma
Ashish Sharma, Senior Manager of Digital for Waste Management, leads the digital solutions team and technology teams in Asset Management's business unit. He is also responsible for the digital team involved in New York's Marine Transfer Station. In 2014, he joined Waste Management. Prior to joining Waste Management, he was a senior leader at Deloitte & Touche, LLC and IBM. He has 16 years of experience working in the technology industry.
Sharma has been involved in many projects while at Waste Management. Recent experience includes working on New York’s marine transfer stations, which was part of Waste Management's $3.3billion contract with Sanitation. Sharma was also awarded the Waste360 40 Under 40 Award. This recognition highlights his leadership skills and innovation in waste management. Ashish Sharma has been awarded a variety of industry awards, including the Waste360 "Best New Product Award".
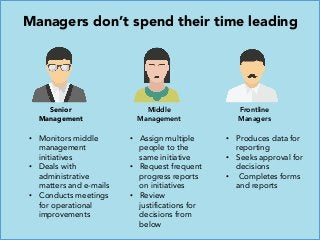
FAQ
What kind people use Six Sigma?
Six Sigma is well-known to those who have worked in operations research and statistics. But anyone can benefit from it.
This requires a lot of dedication, so only people with great leadership skills can make the effort to implement it.
What is Six Sigma?
It's a strategy for quality improvement that emphasizes customer care and continuous learning. This is an approach to quality improvement that uses statistical techniques to eliminate defects.
Motorola invented Six Sigma in 1986 as part its efforts to improve manufacturing.
This idea quickly spread throughout the industry. Today, many organizations use six sigma methods for product design, production and delivery.
What is the best way to motivate your employees as a manager?
Motivation is the desire to do well.
Enjoyable activities can motivate you.
You can also get motivated by seeing your contribution to the success or the improvement of the organization.
For example, if your goal is to become a physician, you will probably find it more motivational to see patients rather than to read a lot of medicine books.
Motivation comes from within.
You may feel strongly that you are responsible to help others.
Or you might enjoy working hard.
If you feel unmotivated, ask yourself why.
You can then think of ways to improve your motivation.
What is TQM, exactly?
The industrial revolution saw the realization that prices alone were not sufficient to sustain manufacturing companies. This led to the birth of quality. They needed to improve quality and efficiency if they were going to remain competitive.
In response to this need for improvement, management developed Total Quality Management (TQM), which focused on improving all aspects of an organization's performance. It included continual improvement processes, employee involvement, customer satisfaction, and customer satisfaction.
Statistics
- Our program is 100% engineered for your success. (online.uc.edu)
- The BLS says that financial services jobs like banking are expected to grow 4% by 2030, about as fast as the national average. (wgu.edu)
- Your choice in Step 5 may very likely be the same or similar to the alternative you placed at the top of your list at the end of Step 4. (umassd.edu)
- 100% of the courses are offered online, and no campus visits are required — a big time-saver for you. (online.uc.edu)
- The profession is expected to grow 7% by 2028, a bit faster than the national average. (wgu.edu)
External Links
How To
How do you apply the Kaizen method to your life?
Kaizen means continuous improvement. The Japanese philosophy emphasizes small, incremental improvements to achieve continuous improvement. This term was created by Toyota Motor Corporation in 1950. This is a collaborative process in which people work together to improve their processes continually.
Kaizen is one the most important methods of Lean Manufacturing. Employees responsible for the production line should identify potential problems in the manufacturing process and work together to resolve them. This is how you can improve the quality and lower the cost.
The main idea behind kaizen is to make every worker aware of what happens around him/her. So that there is no problem, you should immediately correct it if something goes wrong. It is important that employees report any problems they see while on the job to their managers.
Kaizen follows a set of principles. Always start with the end product in mind and work our way back to the beginning. To improve our factory, for example, we need to fix the machines that produce the final product. Next, we repair the machines that make components. Then, the machines that make raw materials. And finally, we fix the workers who work directly with those machines.
This method is known as kaizen because it focuses upon improving every aspect of the process step by step. After we're done with the factory, it's time to go back and fix the problem.
How to measure kaizen's effectiveness in your business is essential to implement it. There are several ways to determine whether kaizen is working well. Another way to determine if kaizen is working well is to look at the quality of the products. Another method is to determine how much productivity has improved since the implementation of kaizen.
If you want to find out if your kaizen is actually working, ask yourself why. Was it just because it was the law or because you wanted to save money? Did you really believe it would lead to success?
Congratulations! You are now ready to begin kaizen.